Renishaw, a leading engineering technology company, has partnered with Cookson Industrial, a UK-based specialist in precious metal additive manufacturing (AM), to reduce the costs associated with 3D printing platinum-rhodium. This collaboration leverages Renishaw’s RenAM 500S Flex AM system, enabling Cookson Industrial to produce high-temperature corrosion-resistant components with improved material efficiency. The advancement is particularly significant for industries such as glass fibre manufacturing, where the viability of using platinum rhodium in additive manufacturing has been enhanced.
Cookson Industrial, a division of Cooksongold and a subsidiary of HM Precious Metals, brings over three decades of expertise in designing and producing precious metal alloys. Faced with platinum rhodium prices averaging £80,000 per kilo, minimizing material waste was essential to make production economically feasible. To address this challenge, Cookson Industrial selected Renishaw’s RenAM 500S Flex, a laser powder bed fusion system designed for research and development in additive manufacturing.
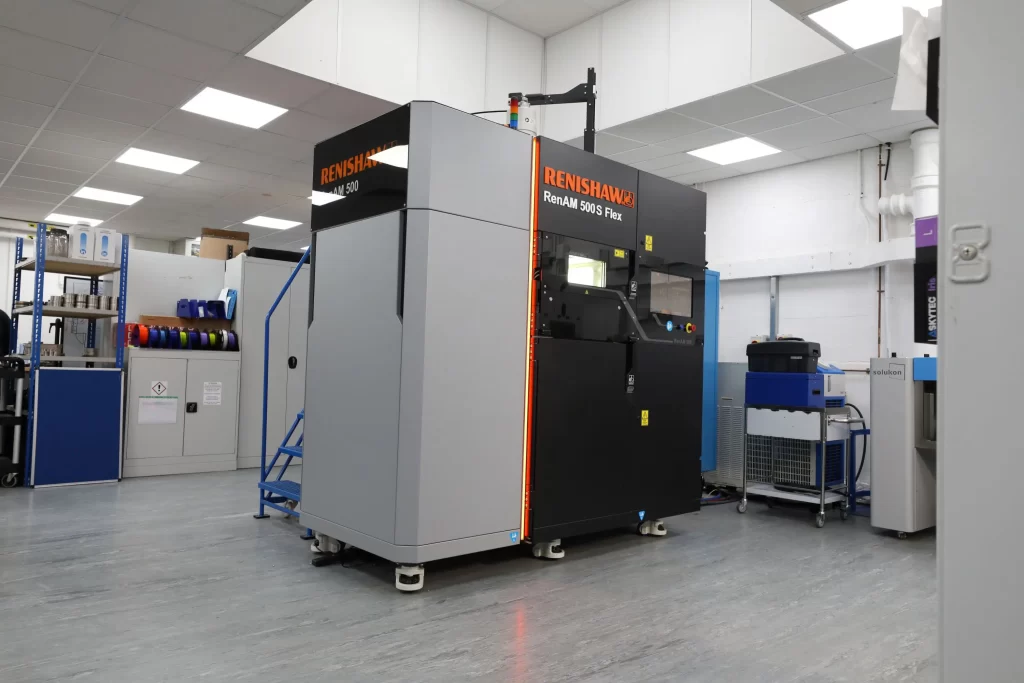
Renishaw’s AM engineering team collaborated closely with Cookson Industrial to adapt the RenAM 500S Flex for platinum rhodium production. While the standard system achieves powder waste levels as low as 1.5%, custom modifications were necessary to reduce waste to below 0.5%. “Achieving near-zero wastage of platinum rhodium powder was a top priority,” stated Jason Morgan, Senior Applications Engineer at Renishaw. “We worked with Cookson’s engineers to identify and eliminate potential powder traps within the system, followed by rapid testing and redesigns to minimize waste without compromising performance.”
The customization process involved modifying internal system components to prevent powder accumulation. This included removing overflow bellows and optimizing the rear overflow vent. Additional measures encompassed chamber redesigns and the creation of specialized casings and covers. These modifications resulted in a 95% reduction in powder waste, allowing Cookson Industrial to recover nearly all platinum rhodium powder. This substantial decrease in material loss translates to significant cost savings and enhances the commercial viability of large-scale production.
Nikesh Patel, Head of Cookson Industrial, commented, “Renishaw’s technology and expertise were crucial to this R&D success, enabling us to produce platinum rhodium parts on a commercial scale. Minimizing powder loss not only reduces our production costs but also makes large-scale manufacturing feasible, saving millions over the machine’s lifetime.”
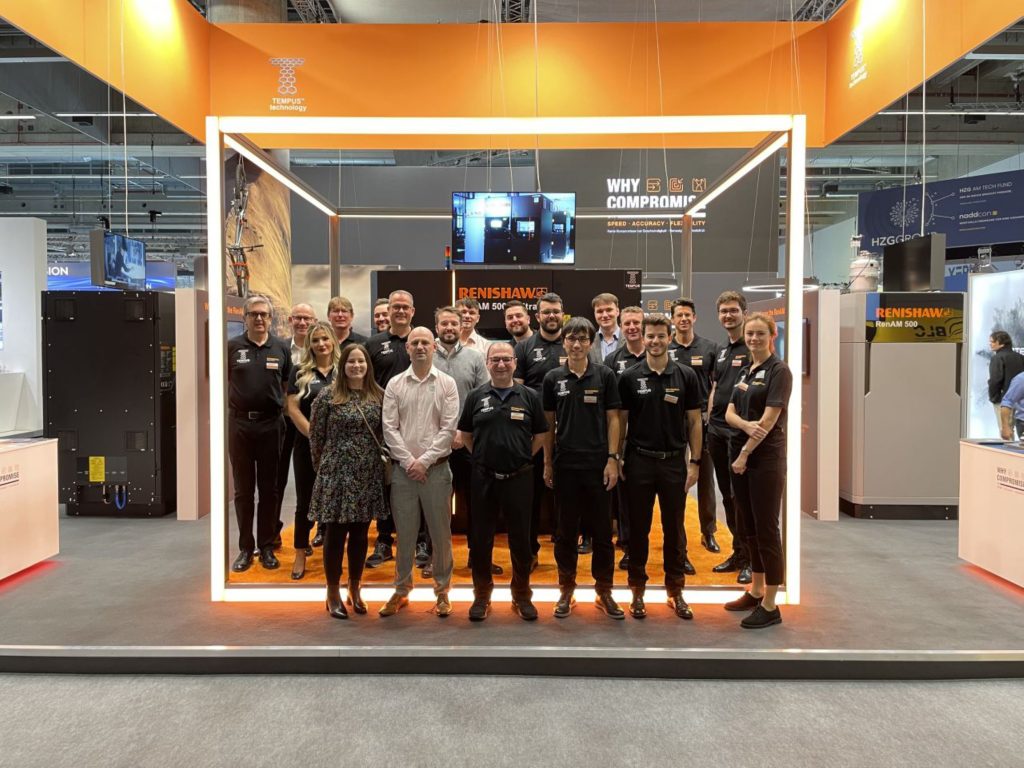
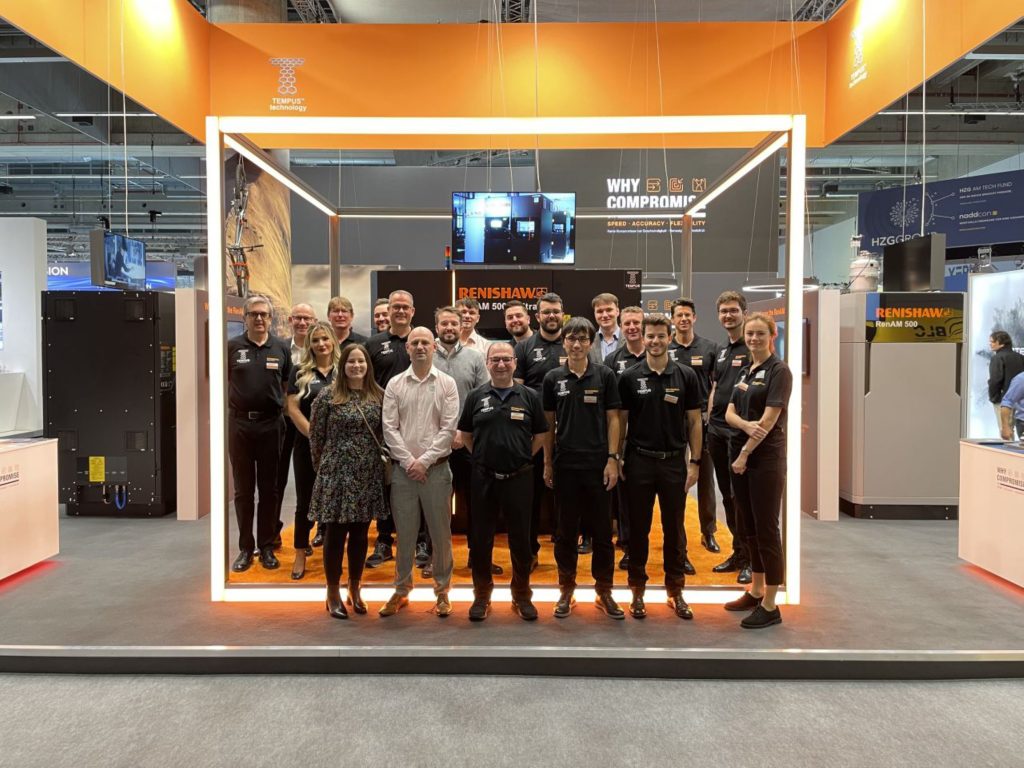
Precious Metals in Industrial AM and Metal Powder Production
Cooksongold recently launched Cookson Industrial, a division dedicated to integrating precious metals into industrial AM sectors such as aerospace and healthcare. Its facility in Birmingham includes multiple EOS Precious M systems and a RenAM 500S Flex, enabling the production of gas-atomized precious metal powders in small batches up to 15kg. A £750,000 grant from the Engineering & Physical Sciences Research Council (EPSRC) supports the development of specialized precious metal alloys at the University of Birmingham, with a focus on extreme environments.
3D Lab, a Warsaw-based service bureau, is introducing the ATO Suite at Formnext 2024. This modular set of equipment manages metal powder production from feedstock preparation to final refinement. The ATO Lab Plus, ATO Noble, and related systems enable custom powder production, reuse of scrap materials, and control over particle size distribution. The equipment occupies a small footprint and includes vacuum casting and ultrasonic sieving options. Such configurations can support the handling of high-value materials by improving powder quality and minimizing contamination.
Your voice matters in the 2024 3D Printing Industry Awards. Vote Now!
What will the future of 3D printing look like?
Which recent trends are driving the 3D printing industry, as highlighted by experts?
Subscribe to the 3D Printing Industry newsletter to stay updated with the latest news and insights.
Stay connected with the latest in 3D printing by following us on Twitter and Facebook, and don’t forget to subscribe to the 3D Printing Industry YouTube channel for more exclusive content.
Featured image shows the RenAM 500S Flex installed at Cookson Industrial. Photo via Renishaw.