Since Shapeways is on the journey of ‘coming home’, we wanted to get to know the people that make the magic happen here in Eindhoven. Every couple of weeks we’ll be speaking to one of the team across the business. Some have been here for many years, others are quite new but they all share a passion for making, improving and supporting each other. This week we caught up with Tistou Geenen, our ‘Continuous Improvement Engineer’ to find out what he does, what motivates him and what he thinks makes for a great Shapie!
“There’s no such thing as a typical day,” says Tistou, Continuous Improvement Engineer at Shapeways’ Eindhoven facility. “Every day starts with a team-wide meeting… if something interesting is happening, then that will be my focus for that day.”
Tistou (or as everyone calls him, Ties) plays a unique role at Shapeways. Officially, he’s a team of one. Unofficially, you’ll find him anywhere and everywhere.
“I have the freedom to prioritise where to take a look at a process or see if we can make something more efficient or automate something,” he explains. “But as soon as that decision is made, I have to work together with the team that’s already doing that process… so in practice, there’s a lot of teamwork.”
Defining continuous improvement
At its heart, his role is about making sure the processes in the factory run as efficiently as possible. That might mean automation, data visualization, or quality assurance — and often all three in the same day. “The end product that we produce is the result of the product going through a set of processes,” he says. “So making these processes go faster, more efficiently, or making sure that they are more consistent or more high quality will all directly impact the end product.”
But what stands out in conversation with Tistou isn’t just what he does, but it’s how he does it. His technical mindset is matched by a clear respect for the people around him. “In my experience, the team usually knows best,” he says. “We’ve had multiple instances that data-wise something seemed like a good idea, but then as soon as you talk with the team… they have at least 10 reasons why it’s not a good idea!”
Those interactions are not roadblocks, instead Tistou sees them as the path to better solutions. “Eventually you come to a process improvement or an automation that really works. So it’s super valuable to include the team in the process as well.”
Practice makes progress
Tistou started at Shapeways while still in school, working in production. After finishing his studies in applied mathematics, he returned full-time and was offered the chance to try something new. “I did not really recognize the opportunity that was here for me. It was really the management that reached out and said, ‘hey, we think you would be a really good fit for this’… I had no idea what being a continuous improvement engineer would entail or how that would look. So I needed a lot of guidance at the start. But I definitely got it.”
Since then, he’s grown into the role and made it his own. “I think you really have to be flexible. Since we are working in the additive industry, every day is different. Every day you have different models for different customers that pose different challenges. That can be super exciting, and that also means that you really have to be on your toes.”
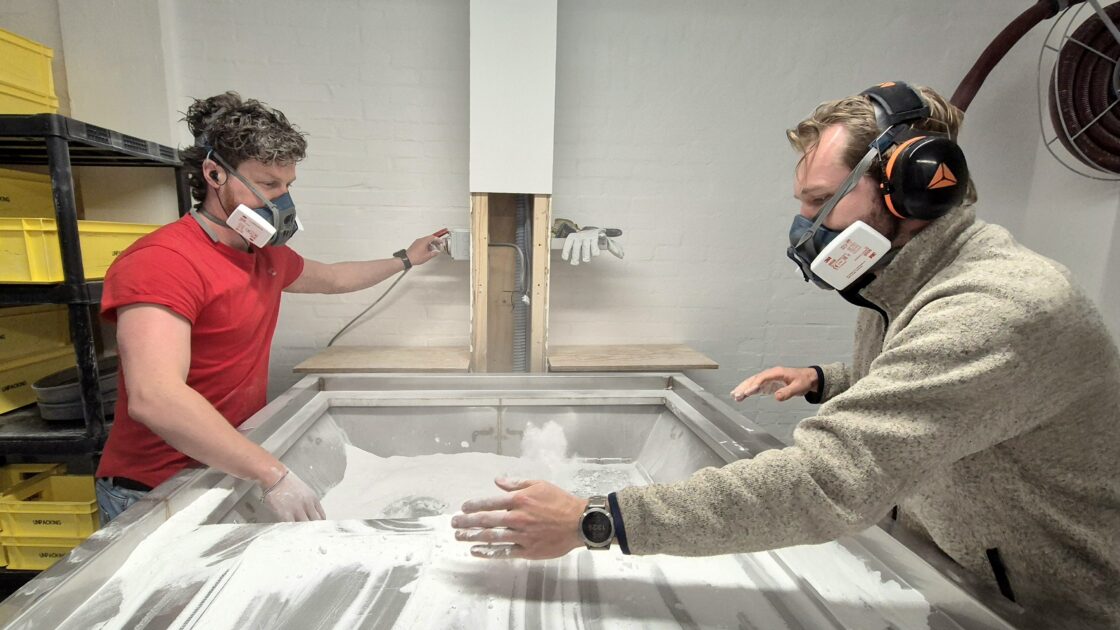
He thrives on it. “I have a little bit of a competitive nature,” he says. “So I can also be competitive against the process. I really like if a number goes up… really seeing that impact, and having the data to see if this is actually working — that’s really a big driver for me.”
One of his proudest examples? “We have some processes that we started work on three years ago… that were done every day by four people. It was also maybe not the most fun work. If you look at it right now, the same process is done by one person in half a day, and it’s fairly enjoyable. And those four people can now focus on something else that really drives us forward.”
Progress must be aligned with people
It’s easy to assume continuous improvement is all about speed and efficiency, but Tistou’s approach is also about culture and experience. “It’s a driver for me, but I think it’s a driver for the team as well. There’s lots of days that I’ll just put on my work shoes and go and work in production… to get a good sense and a good understanding of what is working well, what is not working well.”
“There’s nobody telling anybody, ‘hey, this is how it’s done and there’s no room to have an opinion’. It’s basically the other way around… we want the people that are in the process every day to stand up and say, hey, I think we can do this better.”
That sense of shared purpose runs throughout the Eindhoven site. “We share this big responsibility of getting the product out to the customer every day,” he says. “So even though you might be a small piece of the puzzle… if push comes to shove, and we need you to do something else for a day to make sure that we meet our promise to the customer, then we have to work as a team and make sure that we change things up.”
So what kind of person thrives at Shapeways?
“I think you need to be very enthusiastic and driven to want to learn as much as you can,” says Tistou. “Of course your role is important… but the people that really thrive are the people that also think ‘what’s adjacent to my role, and how can I learn about those processes as well?’”
Every day might look different for Tistou, but the goal stays the same: help the team deliver better parts, faster, while making the process more rewarding for everyone involved. “If you can find something that delivers a better product to the customer faster, but also makes the whole production process more enjoyable… then the team will be fully behind you.”
You can follow along with the Shapeways Team Spotlight series to find out more about the team behind the scenes.
