Improving Injection Molding Efficiency with Conformal Cooling
Founded in 2007, Eastern Rail Corporation built a reputation on designing sustainable, high-quality solutions for the Metro Rail infrastructure in the US. For a specific component—an insulator that isolates the electrified third rail in underground subway systems–Eastern Rail needed to update the material to meet safety standards. A switch to Polyphenylene Sulfide (PPS) subsequently required a reevaluation of the existing mold. To tackle this issue, Eastern Rail approached Linear AMS, a Shapeways Company, seeking partnership in creating an innovative solution to enhance functionality and efficiency.
Eastern Rail is a long-standing customer, supporting transit agencies in metropolitan areas like New York City, Washington, D.C., and Miami, where urban rail systems frequently operate in underground tunnels. Such an environment demands components with specific dielectric properties, safeguarding against unwanted electrical charges and allowing for more effective management of underground train lines.
Incorporating Advanced Cooling Technology
Injection molding manufacturers often face challenges related to long cycle times, part quality, and overall efficiency. Conformal cooling technology specifically resolves these problems. Relying on 3D printing for customization and efficiency, conformal cooling adapts to fit into industrial molds.
In contrast to conventional methods, which are restricted to machining in straight lines, conformal lines are designed to follow the shape of the part itself–leading to a more consistent temperature throughout the part’s cooling stage. This means that parts are less likely to warp, while also cooling up to 50% faster. With conformal cooling, manufacturers can reduce their cycle time and increase their throughput, all while improving part quality.
For Eastern Rail, integrating this technology produced more consistent temperatures in tooling, leading to more efficient production cycles, satisfying stringent requirements for reliable and efficient rail systems.
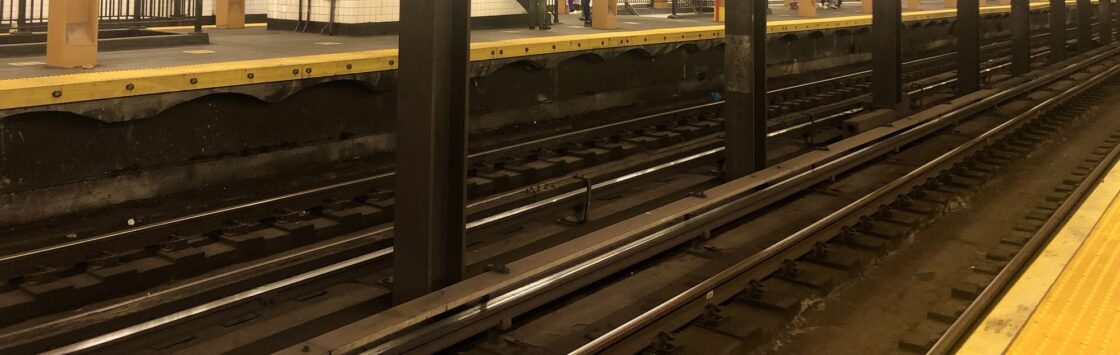
Improving Tooling for Complex Materials
Initially, Eastern Rail encountered challenges due to the complex part design and core mold features, combined with the nature of Xencor PPS LGF-3045, a 45% long-glass, fiber-reinforced Polyphenylene Sulfide (PPS).
While providing beneficial properties like heat resistance and durability, PPS also presents manufacturing difficulties. Linear performed a comprehensive analysis, revealing that Eastern Rail’s existing tooling with conventional cooling–in combination with a PPS material–would not produce a moldable part.
“I was aware a new approach would be necessary with the change in material,” said Mickey Morales, CEO of Eastern Rail. “After working with Linear for the past decade, I was confident in their engineering expertise and knew they were capable of delivering the dynamic solution this project needed.”
To address these issues, Linear and Eastern Rail worked side-by-side for months in prototyping and testing, experimenting with molds and the integration of 3D printed conformal cooling lines.
Upon initial review, the team suggested making the change to a steel mold over aluminum for production volumes. The PPS material is highly corrosive and would deteriorate the aluminum mold. Transitioning to a steel mold also opened up the possibility of using conformal cooling to allow for better thermal control. Additionally, based on the molding temperature requirements of PPS, the team determined hot oil would be necessary to maintain tool temperature, as opposed to water which is more commonly used.
“The shift to steel molds significantly transformed our approach, working much better with the unique characteristics of PPS and the need for a precise, controlled molding environment,” said John Tenbusch, Director of Automotive Sales at Shapeways.
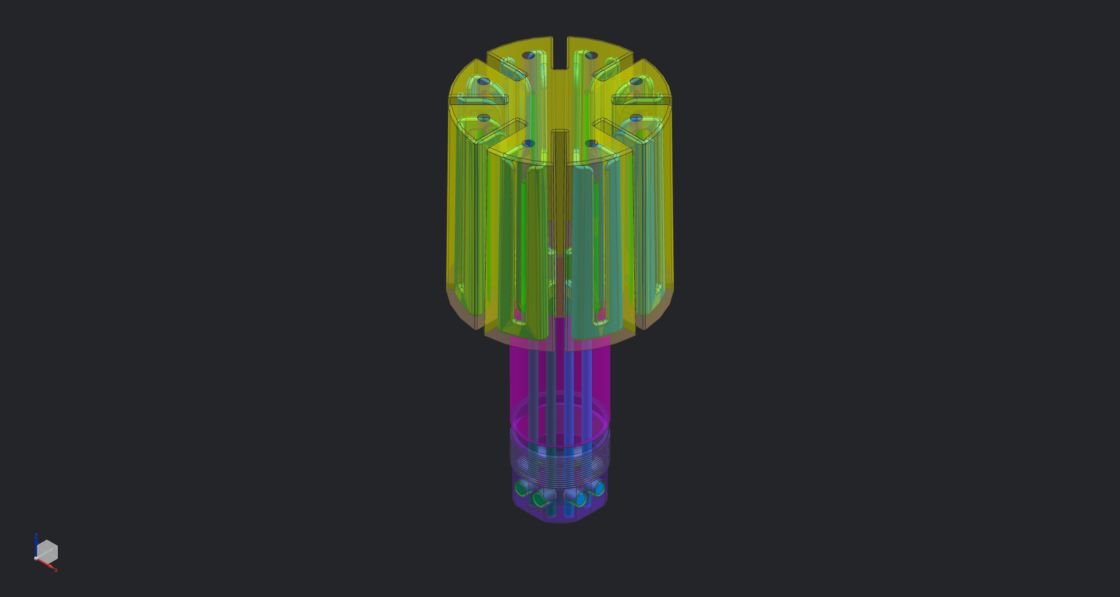
“After working with Linear [A Shapeways Company] for the past decade, I was confident in their engineering expertise and knew they were capable of delivering the dynamic solution this project needed.”
Mickey Morales, CEO of Eastern Rail
Reducing Cycle Times & Improving Part Quality
The introduction of conformal cooling was highly effective, yielding a remarkable improvement in efficiency after Linear introduced steel tooling. Implementing conformal cooling led to a design adjustment that significantly cut costs. Interchangeable inserts, usually requiring three cores, were reduced to just one.
“We had to incorporate cooling one way or another,” said David Dickerson, Manager of Client Services at Shapeways. “Without conformal cooling, we couldn’t have made the interchangeable parts we needed for the various sizes of the insulator.”
With the new steel molds and conformal cooling inserts, the Linear team was able to reduce the cycle time from 181 seconds to 138 seconds, reflecting a 23% improvement. Reduced production time allows for more parts to be made, lowering both piece cost and overall program cost, without sacrificing part quality. The more even, controlled temperatures also led to the production of higher-quality, more reliable parts.
While the initial prototyping and testing phase required significant time and financial investment, the cost savings over the long term more than justified the upfront expenditure. The enhanced material durability, lower maintenance needs, and increased production speeds collectively contributed to significant long-term economic advantage for Eastern Rail.
“While we encountered a few obstacles during our journey, Linear’s team of experts was again able to provide a highly engineered solution while providing cost-saving benefits,” said Mickey Morales, CEO of Eastern Rail.
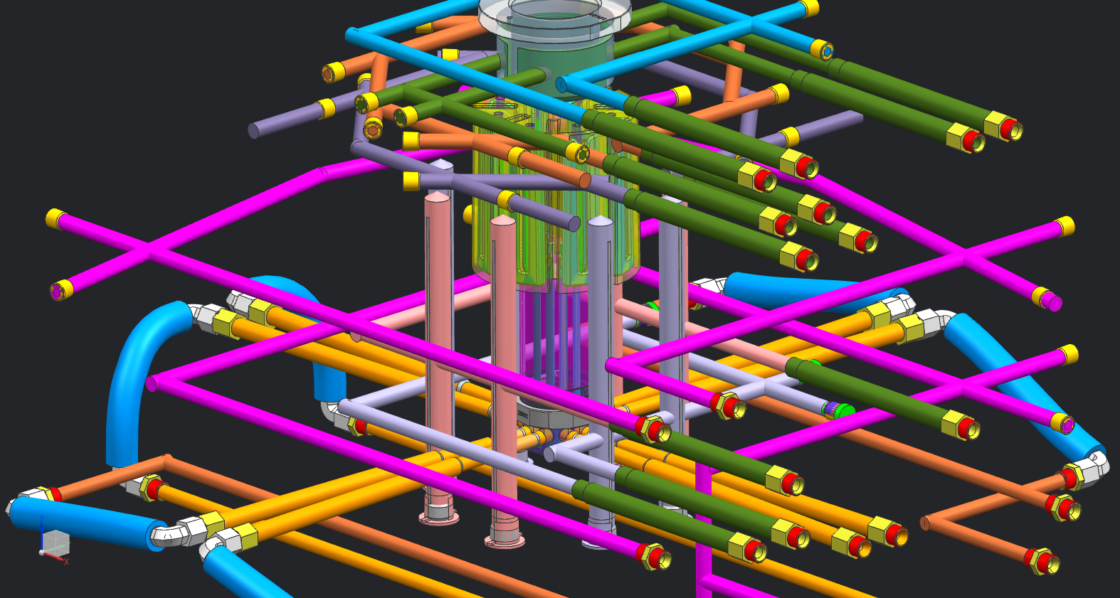
Aligning with Regulatory and Environmental Considerations
Eastern Rail’s openness to new solutions enabled improvements with both short and long-term benefits, meeting industry-specific needs while maintaining a commitment to environmentally friendly materials and regulatory compliance.
This case study offers useful problem-solving insights for issues related to materials, tooling, and cooling. These solutions may be applicable to other manufacturing sectors as well. Overall, this project showcases the value of teamwork, innovation, and excellence in manufacturing
Find out more about how Shapeways can collaborate with your company.
The post Case Study: Eastern Rail Corporation appeared first on Shapeways Blog.