AMAZEMET, a Warsaw-based company, is preparing to launch its Powder2Powder (P2P) atomization system at the Formnext 2024 event. Designed for the additive manufacturing (AM) industry, the P2P system offers a streamlined approach to recycling metal powders and producing tailored pre-alloy powders directly from powder feedstock.
The P2P system combines plasma processing with ultrasonic atomization to convert irregular or oversized particles into highly spherical, satellite-free powders optimized for AM applications. This process (see Figure 1) allows powder size to be controlled independently from the initial feedstock’s characteristics. The P2P technology, uniquely, facilitates the direct atomization of pulverized titanium (Ti) feedstock, making it a distinctive solution in metal powder production.
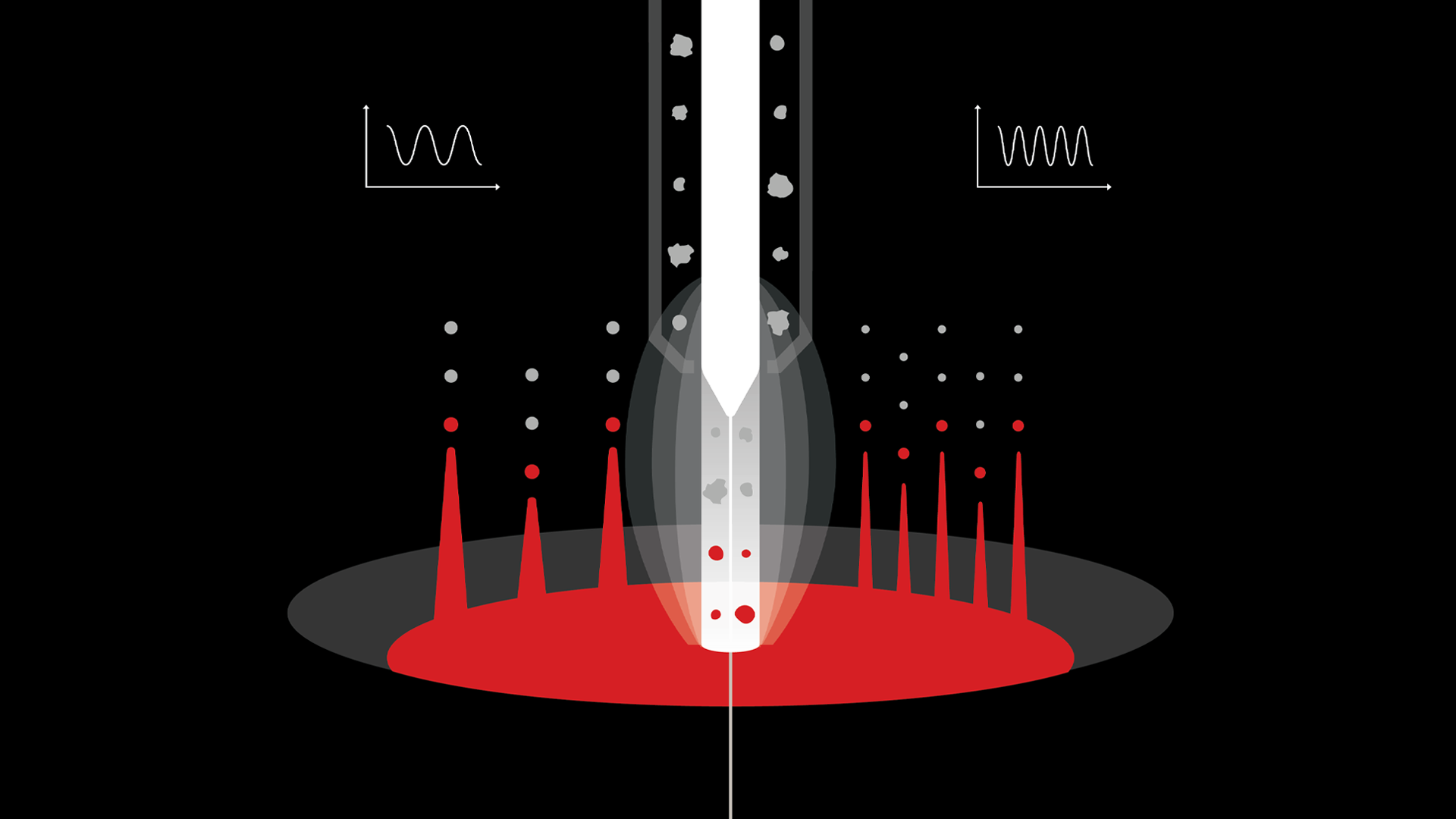
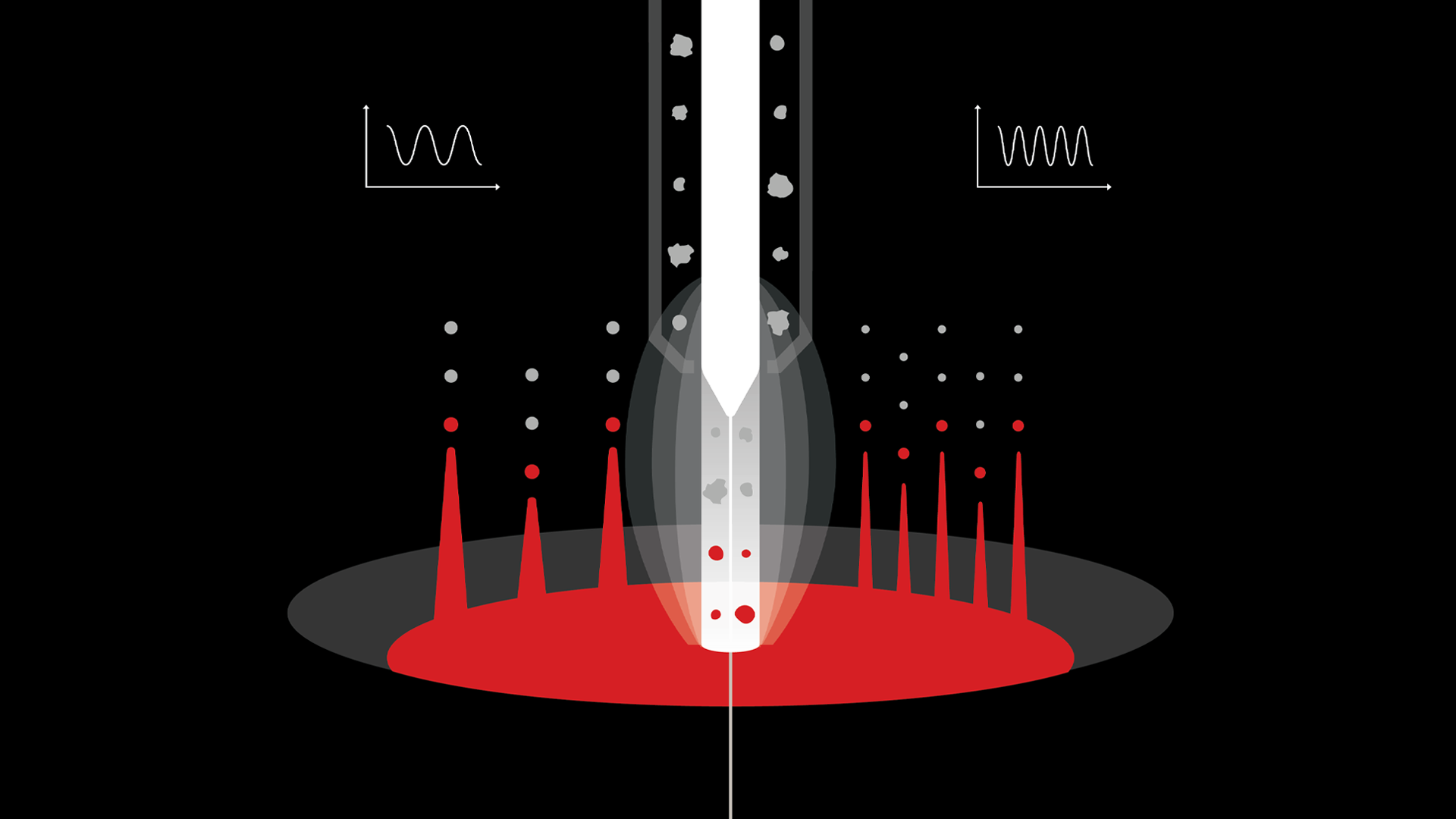
Performance and Efficiency in Testing
AMAZEMET conducted extensive testing on +200 μm oversized and irregular titanium alloy powders, demonstrating the system’s capabilities. Operating at 40 kHz, the P2P system achieved a powder morphology with an aspect ratio (D50) exceeding 0.95, and controlled particle size distribution (PSD) with a D90 < 80 μm. The tests resulted in powder particles <63 μm at an impressive yield of over 80%, with nearly 97% of the resulting powder being suitable for AM techniques, such as Laser Powder Bed Fusion (LPBF), Directed Energy Deposition (DED), and Electron Beam Melting (EBM). This efficiency highlights the system’s potential to support sustainable powder production by optimizing the use of feedstock.
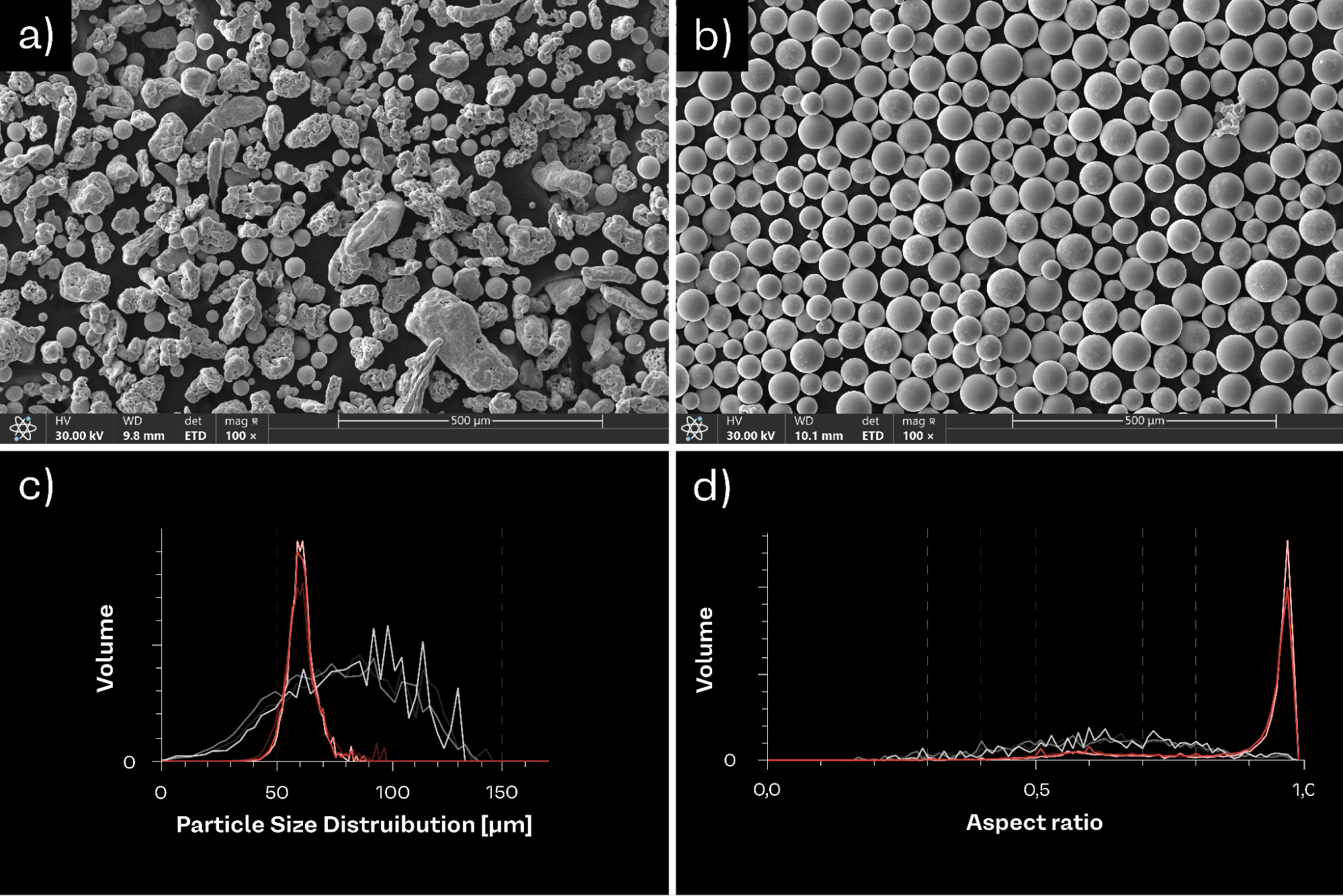
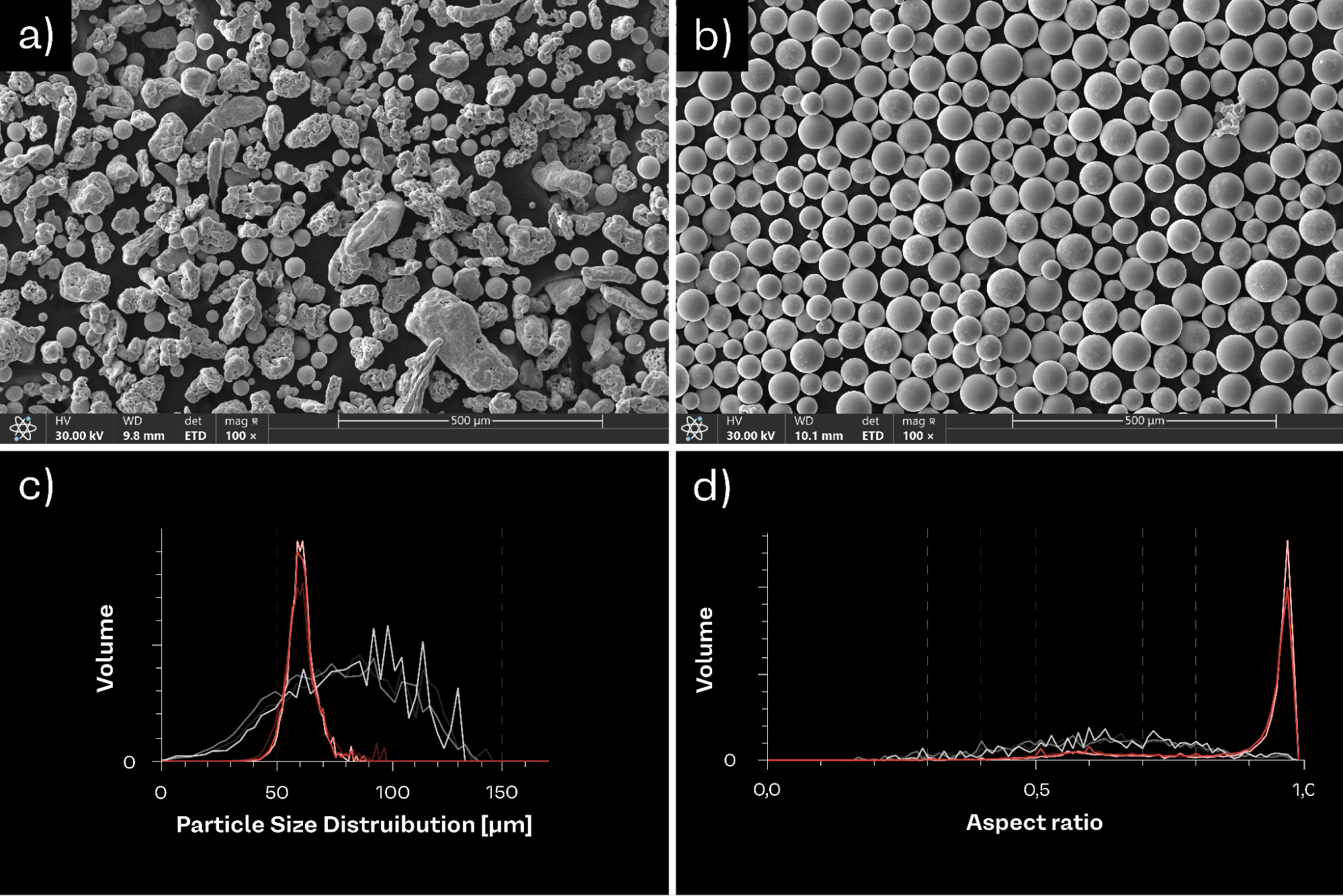
In addition to recycling, the P2P system can process combinations of elemental powders to create pre-alloyed materials with specific chemical compositions. This capability serves both research and industrial purposes, enabling tailored material production. AMAZEMET’s trials with a Ti and 10% wt. Mo blend showed successful alloying, with both refractory elements forming homogeneous powders. This patented technology, scheduled for release in early 2025, directly addresses AM industry challenges of upcycling powder waste and creating custom powders, providing advanced functionality compared to traditional recycling methods.
Key Features of the Powder2Powder System
- Particle Size Distribution Control
The system adjusts PSD, transforming oversized and undersized particles into AM-compatible powder optimized for LPBF, DED, and similar technologies. - Powder Morphology
Combining plasma technology with ultrasonic atomization, the system converts irregular powders into spherical, satellite-free particles that improve performance in AM processes. - Powder Alloying
Elemental powder blends or commercial alloys with minor additions can be directly atomized without preprocessing steps. Unlike other atomization processes, such as EIGA or plasma atomization, new alloys can be developed rapidly without electrode casting or wire drawing. - Multi-Material Capability
The P2P system handles a diverse range of metal powders, including steel, titanium, nickel, refractory alloys, and high-entropy alloys (HEAs), enabling production of powders for various AM applications. - Sustainability and Efficiency
By converting unusable powders into AM-ready material, the system reduces waste and promotes sustainable manufacturing practices.
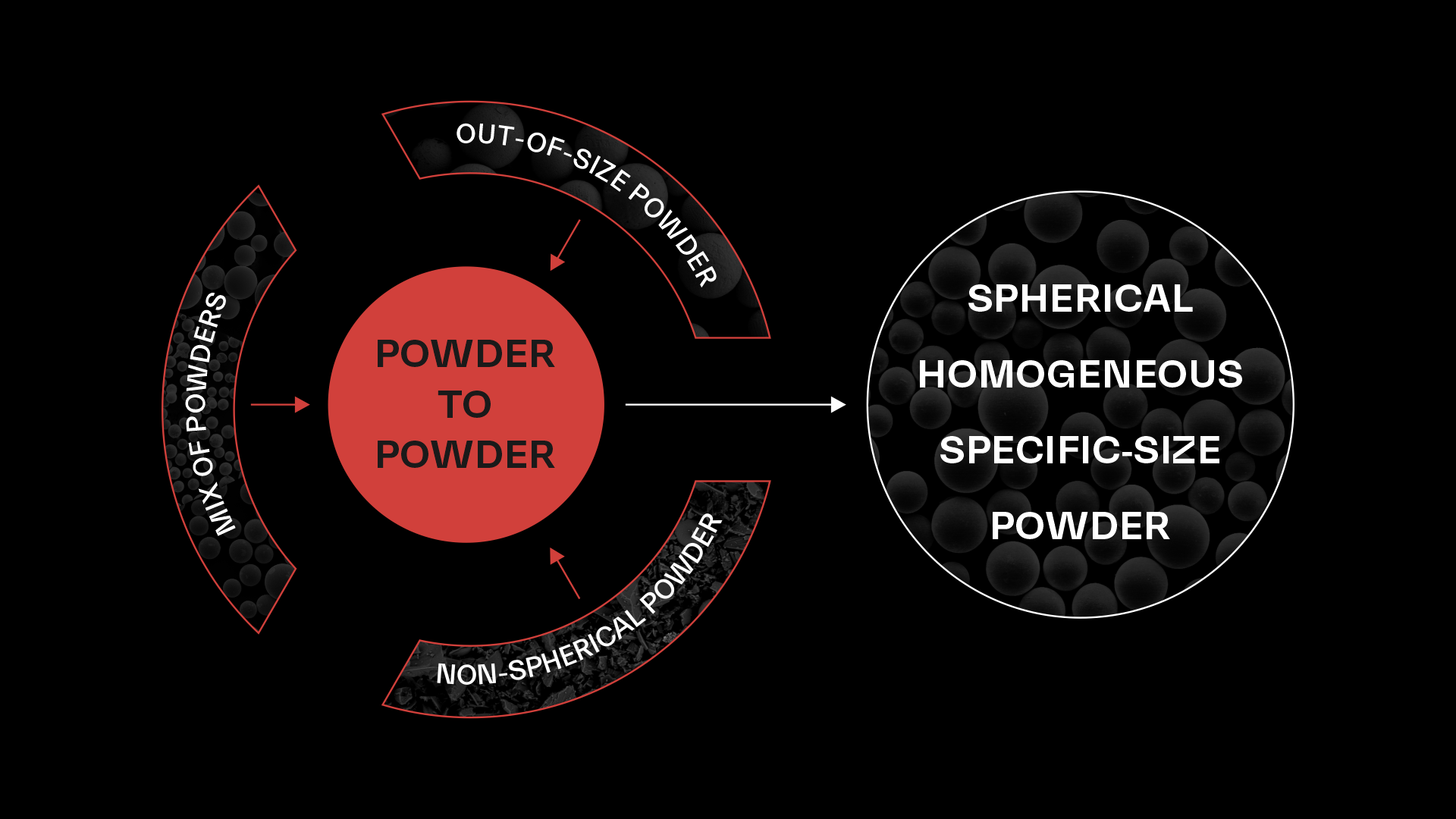
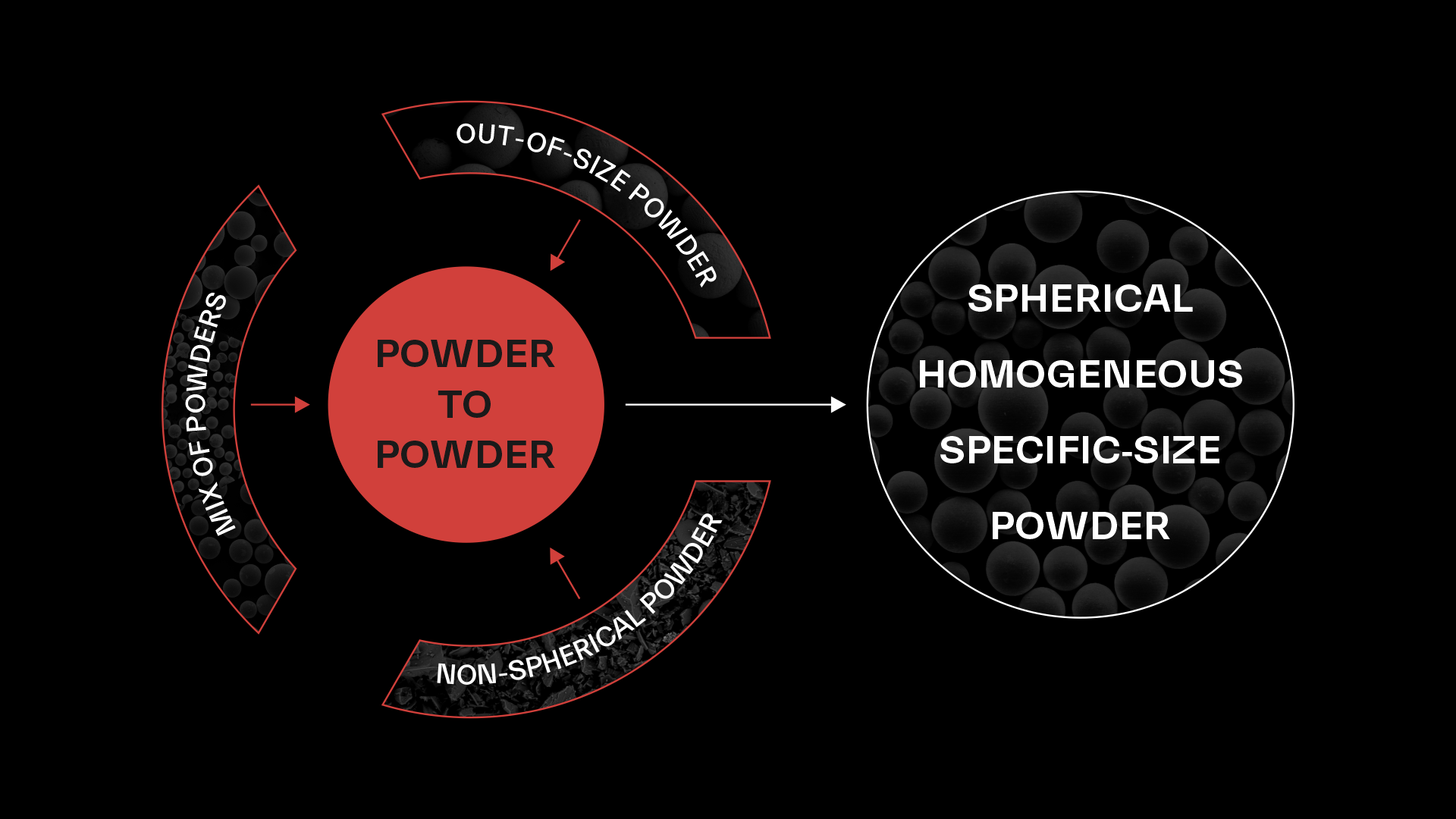
Statement from AMAZEMET’s CEO
Łukasz Żrodowski, the inventor and CEO of AMAZEMET, describes the P2P system’s unique approach: “The Powder2Powder system goes beyond recycling. It gives manufacturers the ability to customize powder compositions, improve powder sphericity, and optimize particle size distribution, solving critical issues in the AM industry. We’re excited to debut this at Formnext 2024, where we’ll showcase how it can enhance the efficiency and sustainability of powder-based manufacturing.”
Formnext 2024 attendees will have the first opportunity to see this technology in action. The P2P system provides an all-in-one solution for recycling and custom alloy powder production, offering manufacturers a new tool for additive manufacturing. More information on the Powder2Powder system will be available at p2p.amazemet.com.
Visit AMAZEMET at FORMNEXT 2024 – Hall 12.0, E61, see the interactive floorplan.