Thailand is making significant strides in sustainable construction with the development of its second 3D-printed prefabricated modular building. The work of SCG Cement Co.,Ltd is centered around the use of low carbon mortar formulas. These advanced concrete materials have been specifically engineered to reduce the carbon footprint of construction, demonstrating a commitment to both environmental sustainability and innovation in the field of 3D printing.
The project’s focus on integrating low carbon mortar with 3D printing technology showcases how the construction industry can move towards more sustainable practices. By combining SCG Cement’s low-emission concrete formulas with cutting-edge 3D printing, this initiative is setting a new standard for eco-friendly building solutions in Southeast Asia.
Low Carbon Mortar: A Sustainable Foundation for 3D-Printed Structures
One of the standout features of this project is the use of low carbon mortar, a specialized concrete formula developed by SCG Cement that significantly reduces the carbon emissions associated with traditional concrete production. As the leading supplier of concrete in Southeast Asia, SCG has developed this formula by incorporating alternative materials and waste products that capture and store carbon dioxide, turning what was once waste into a valuable resource.
In this project, low carbon mortar was utilized in the 3D-printed components of the building, specifically in the production of lightweight mortar walls. The concrete’s carbon footprint was significantly reduced while maintaining the structural integrity and durability required for long-lasting buildings. The integration of low carbon mortar into 3D printing highlights the possibilities for reducing emissions in large-scale construction projects without compromising on quality or efficiency.
By reducing the need for traditional cement, which is a major contributor to carbon emissions, this project represents a step forward in creating low-carbon building materials. The 3D printing process also ensures material precision, meaning only the necessary amount of low carbon mortar is used, minimizing waste and further contributing to the project’s sustainability goals.
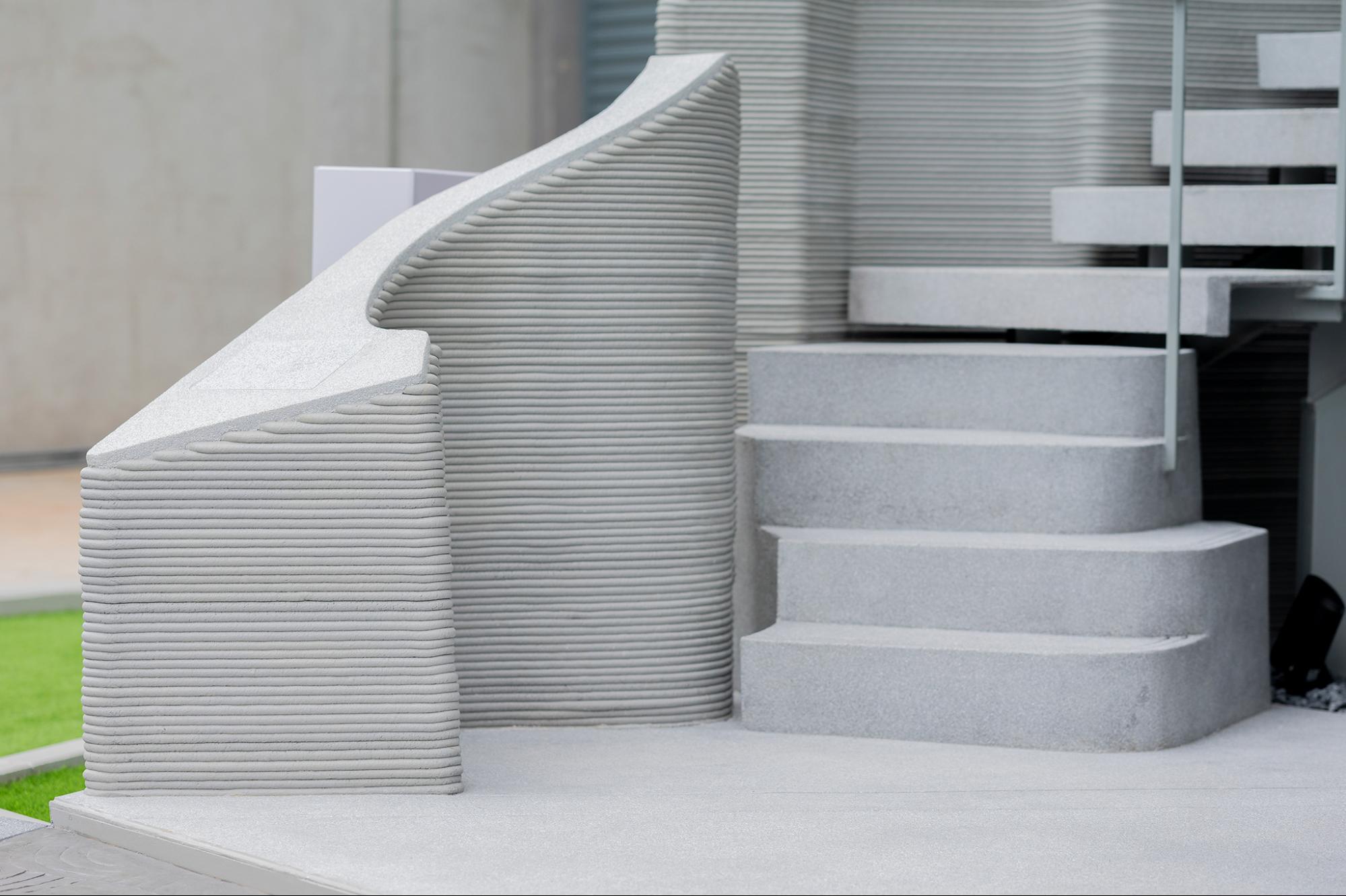
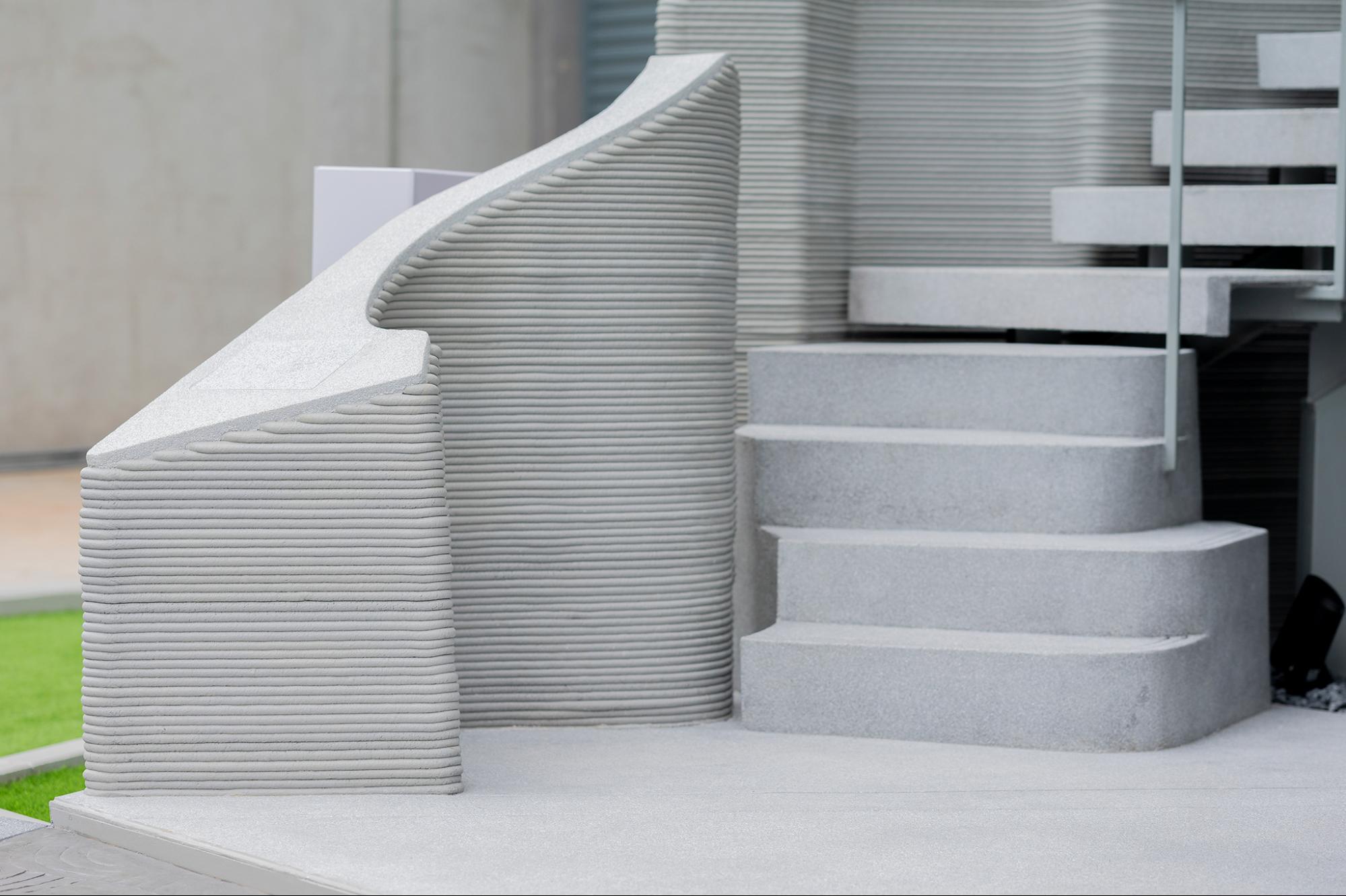
3D Printing and Low Carbon Materials: A Powerful Combination for Sustainable Construction
The combination of low carbon mortar and 3D printing technology brings numerous advantages to the construction process. Using prefabricated 3D-printed modules, the building’s structural elements were produced off-site and assembled on location, drastically reducing on-site labor and construction time. This approach not only improves efficiency but also minimizes the environmental impact by limiting transportation and on-site waste generation.
The use of low carbon mortar in combination with 3D printing marks a significant advancement in sustainable building practices, offering a glimpse into the future of construction. By focusing on reducing the carbon footprint of materials while taking advantage of the efficiency and precision of additive manufacturing, this project serves as a model for how the construction industry can move towards greener, more eco-conscious solutions.
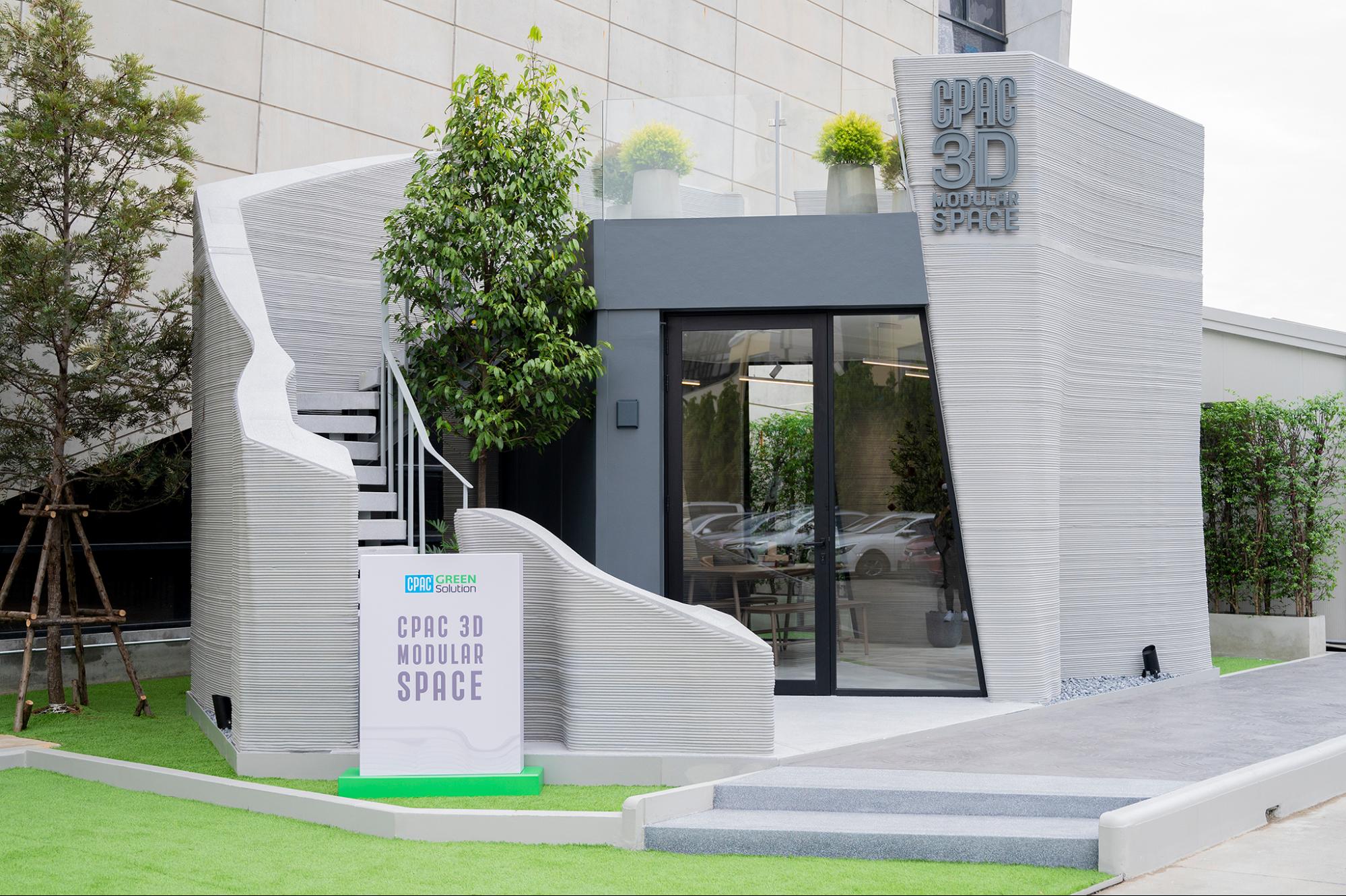
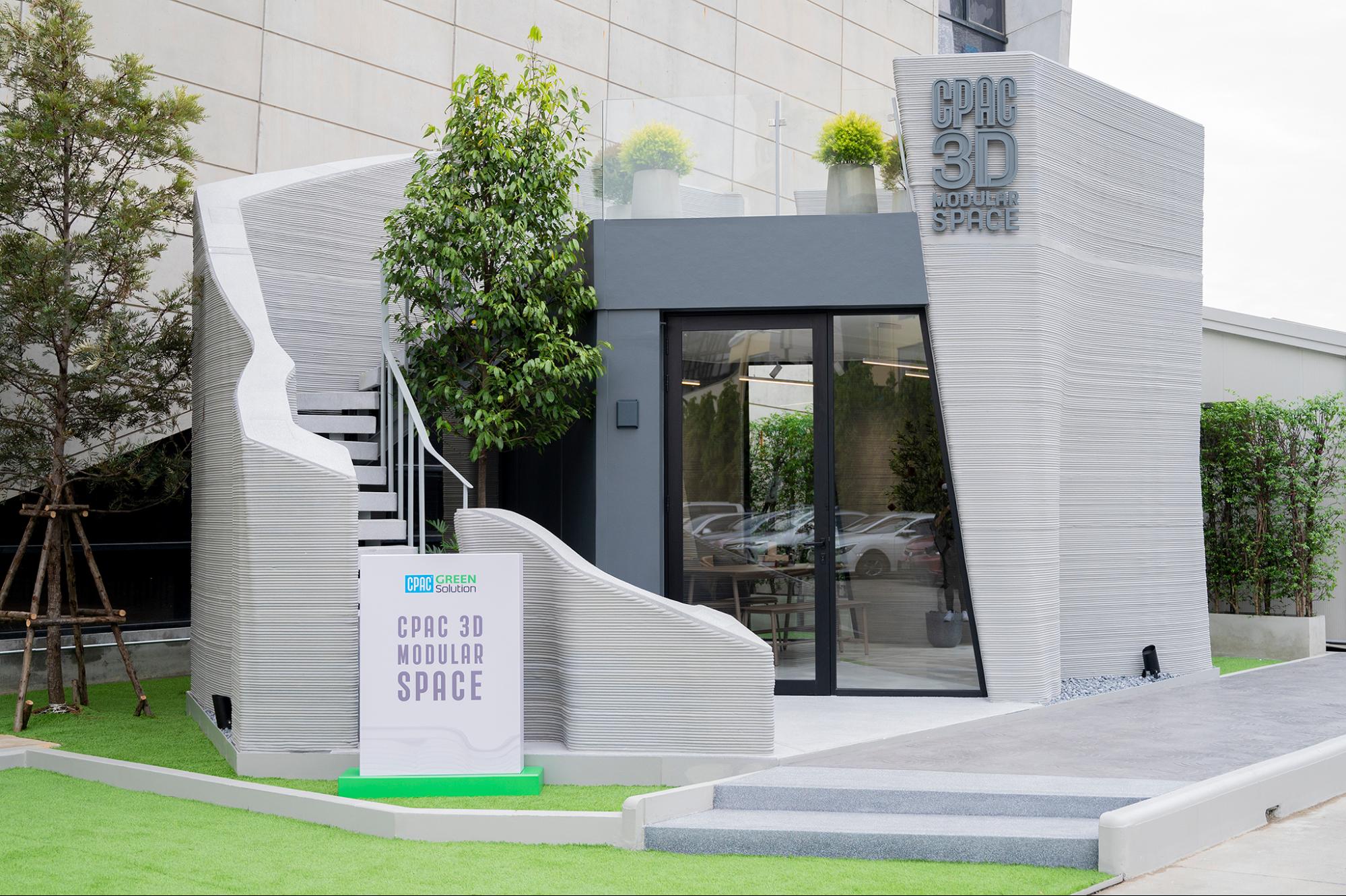
Design of a 3D-Printed Prefabricated Volumetric Building
The innovative building demonstrates the design freedom offered by 3D printing, enabling unique architectural characteristics that traditional construction methods cannot easily achieve. Its distinctive shape, featuring a curved wall, highlights the mold-less design capabilities of 3D printing. With a usable area of 58 square meters, the structure comprises six prefabricated modules, each tailored to specific sizes and functions.


Designed for a public installation site, the weight of each module was limited to a maximum of 10 tons, ensuring ease of transportation and assembly. This modular approach emphasizes practicality while showcasing the flexibility of 3D-printed construction technology.
Concept and Structural Design
Intended for residential use, the building is designed to support a live load of 150 kg/m². Each module integrates a steel frame structure, with sections joined by welding for stability. The dry joint system used to connect the modules forms a moment-resisting frame when assembled, ensuring durability and performance.
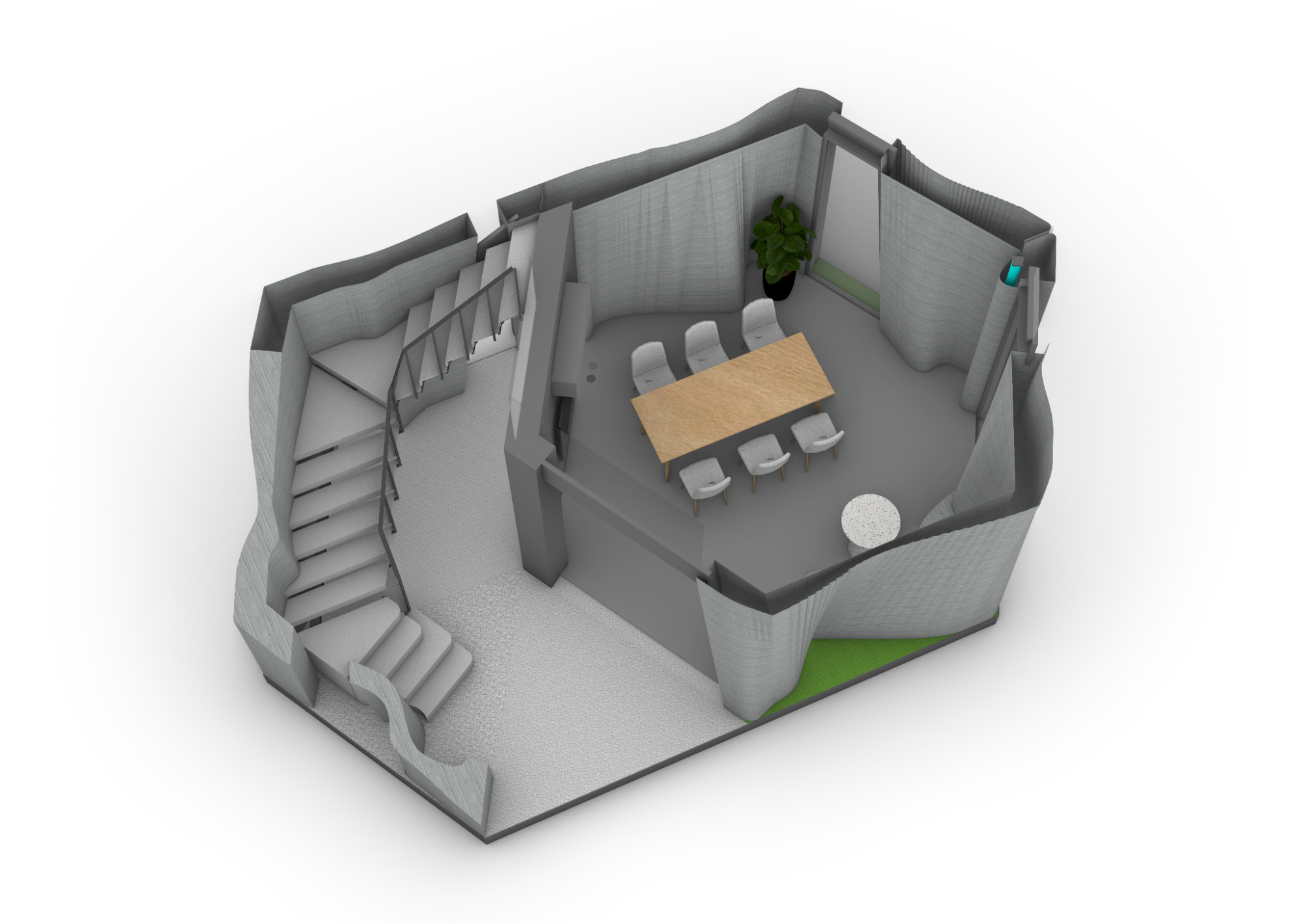
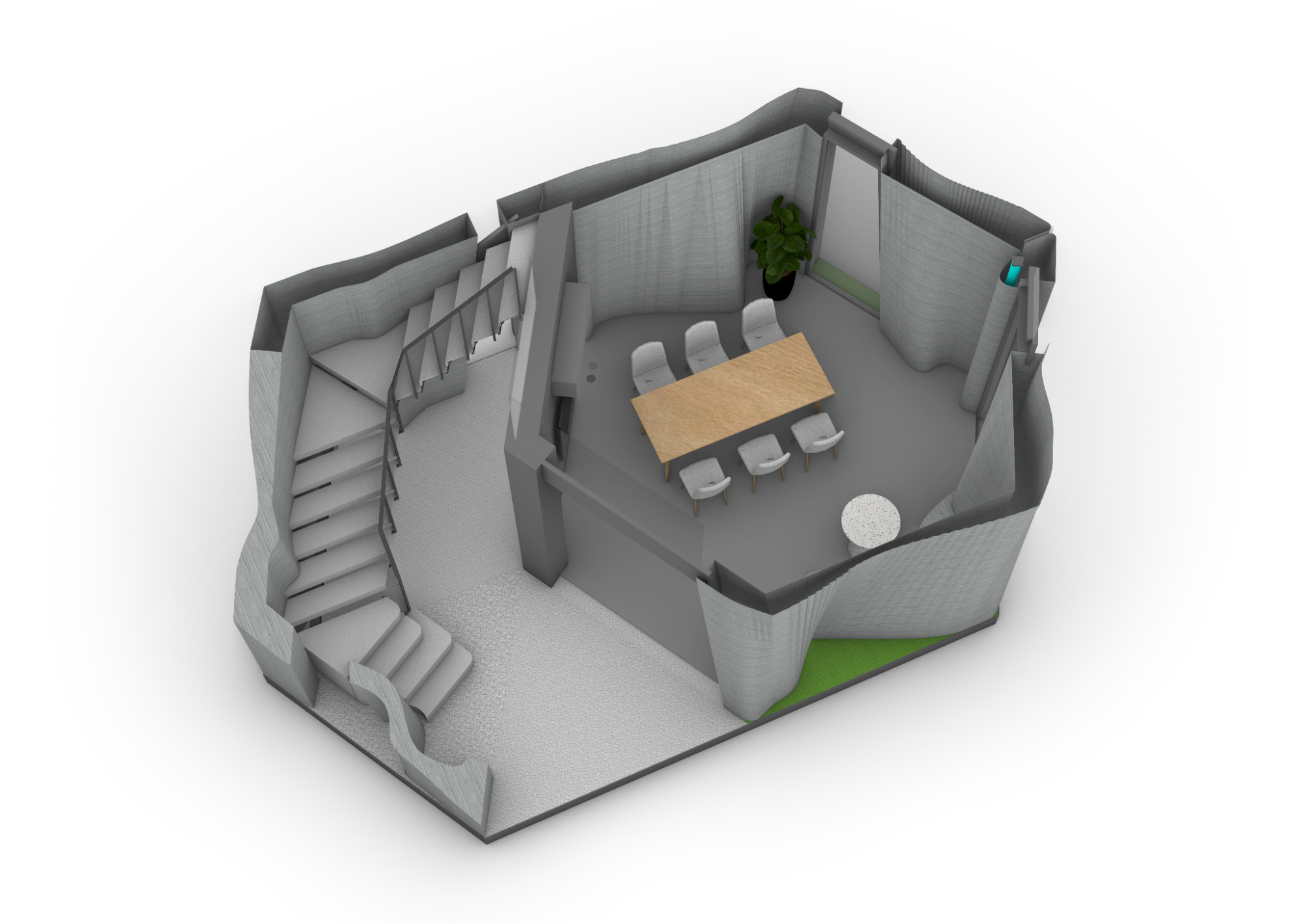
To ensure the safety and integrity of the structure, comprehensive analyses were performed. The steel framework was assessed using Autodesk Robot software, while finite element analysis (FEA) was conducted on the 3D-printed walls. These evaluations incorporated findings from earlier research to examine the structural behavior during lifting, transportation, construction, and usage stages.
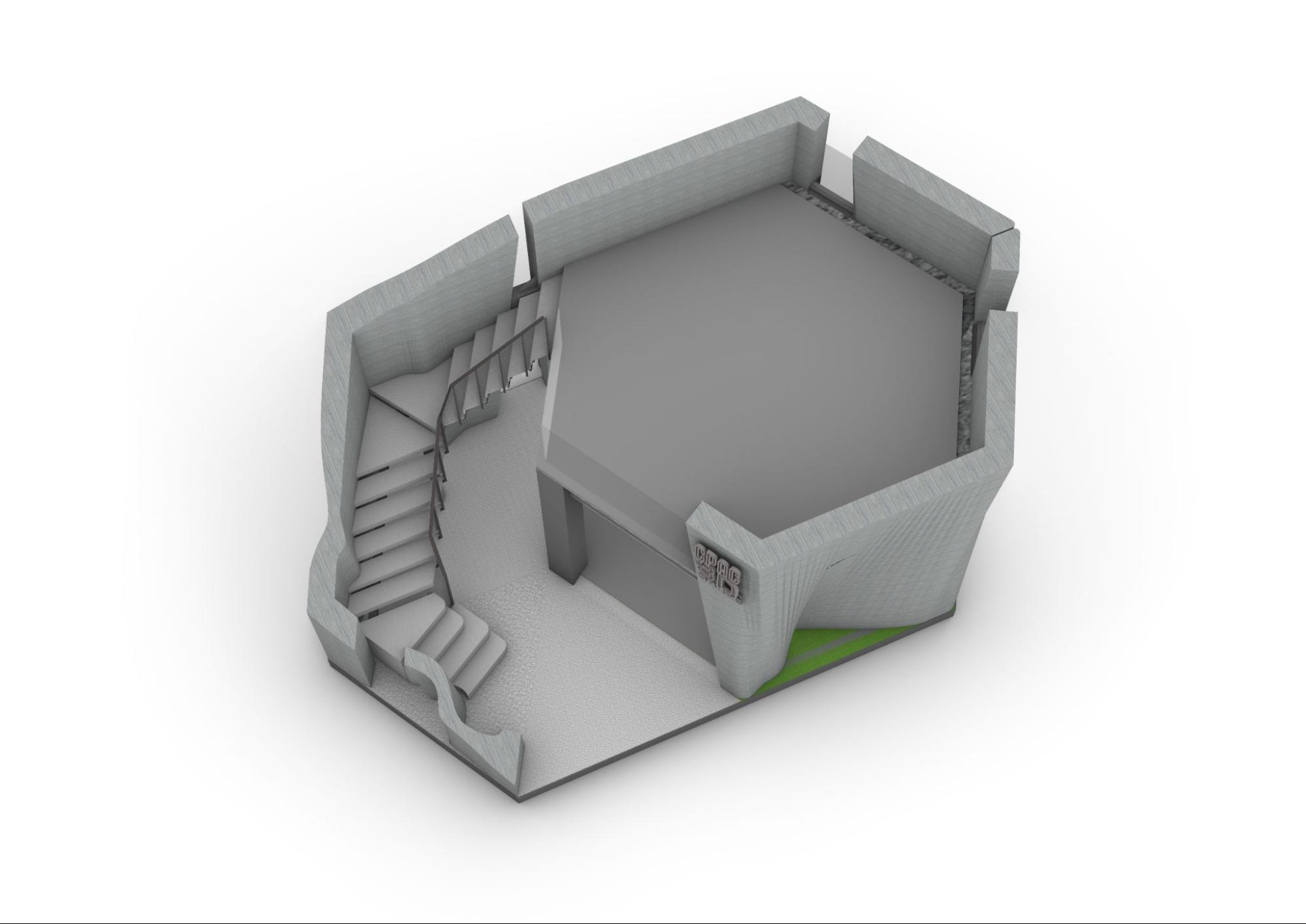
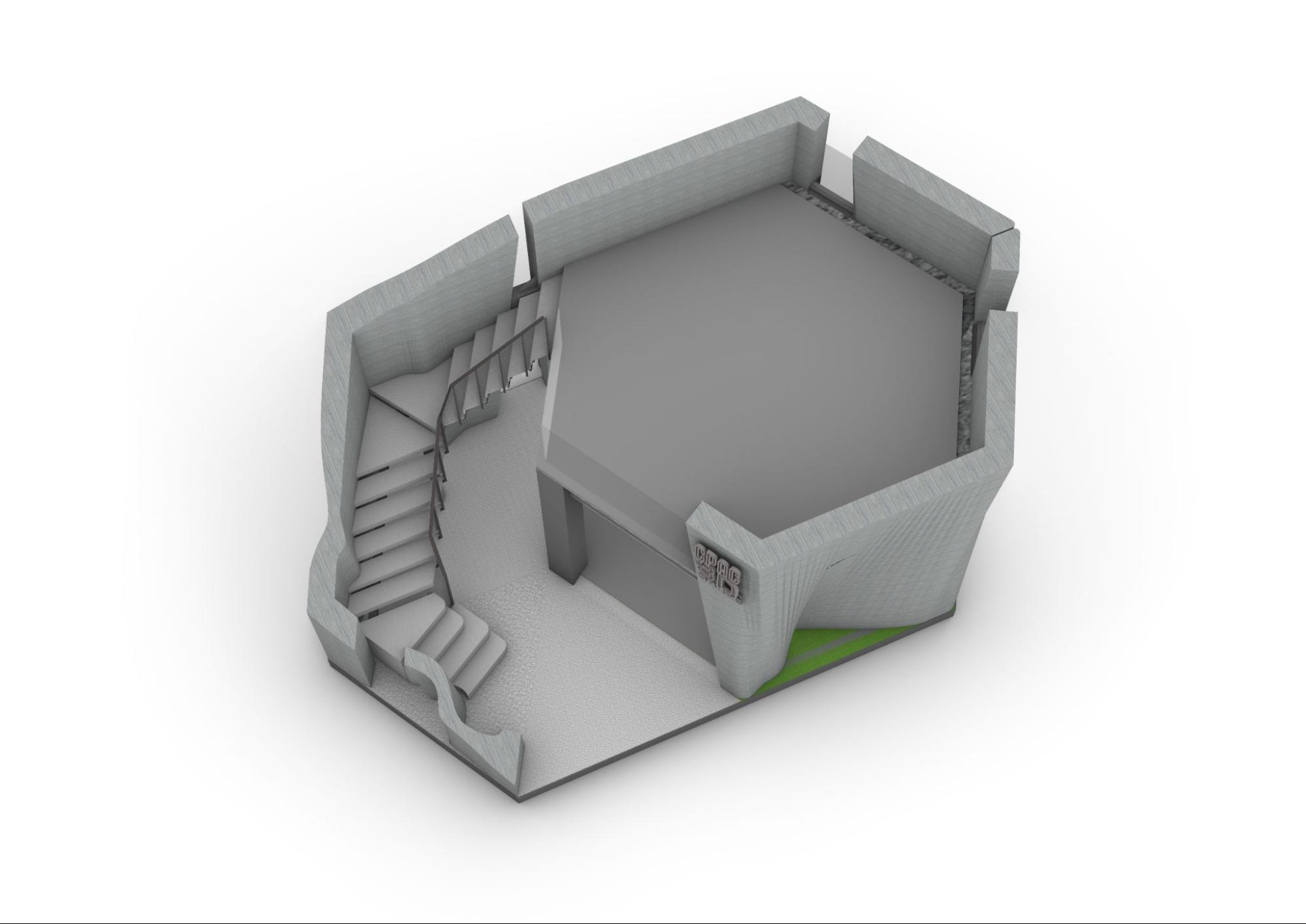
The joint details used in this building follow the design principles of PP3DVC construction, prioritizing strength, leakage prevention, ease of assembly, and aesthetics. Together, these features highlight the synergy between 3D printing and traditional structural elements, setting a benchmark for modern prefabricated building design.
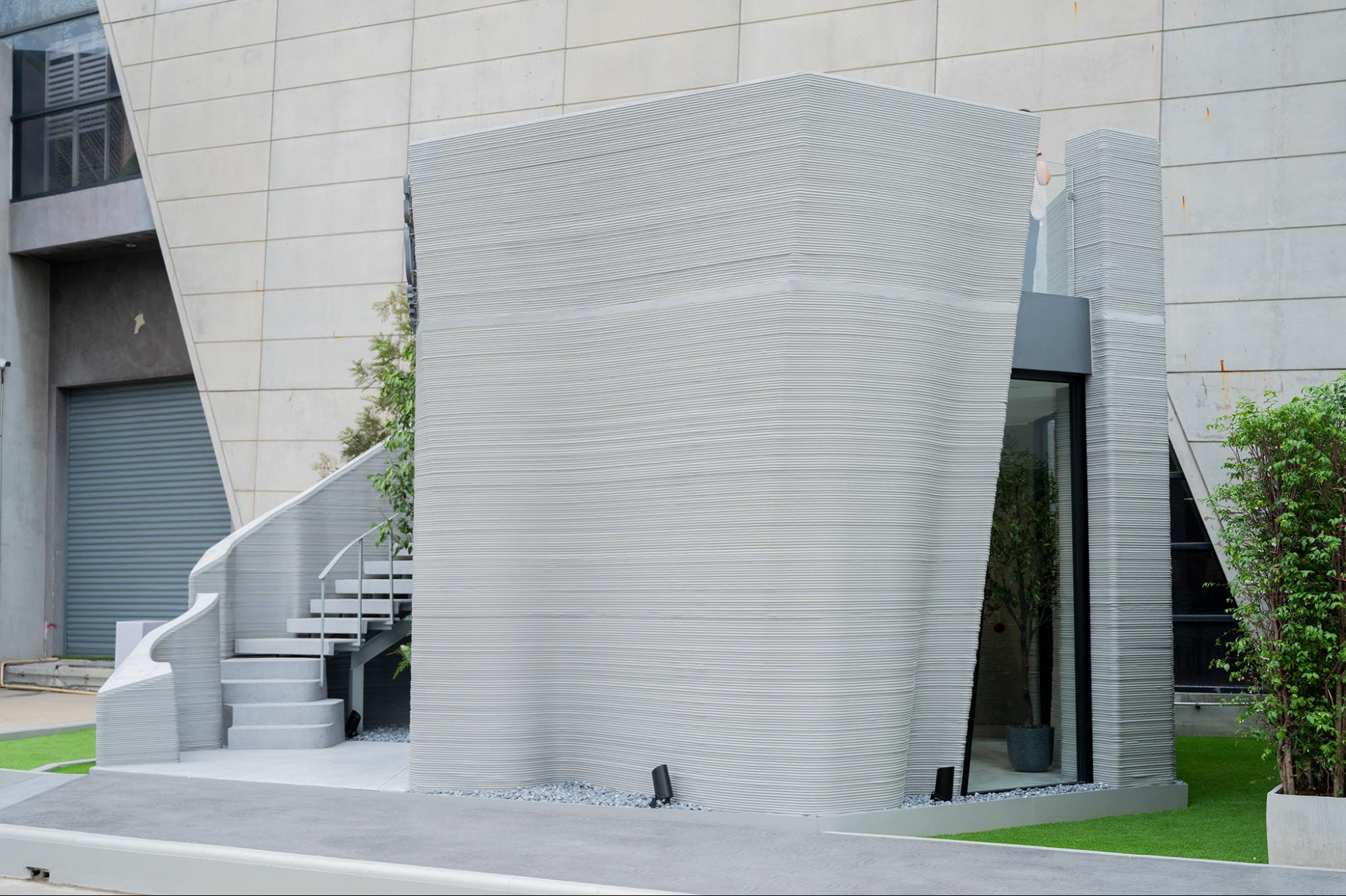
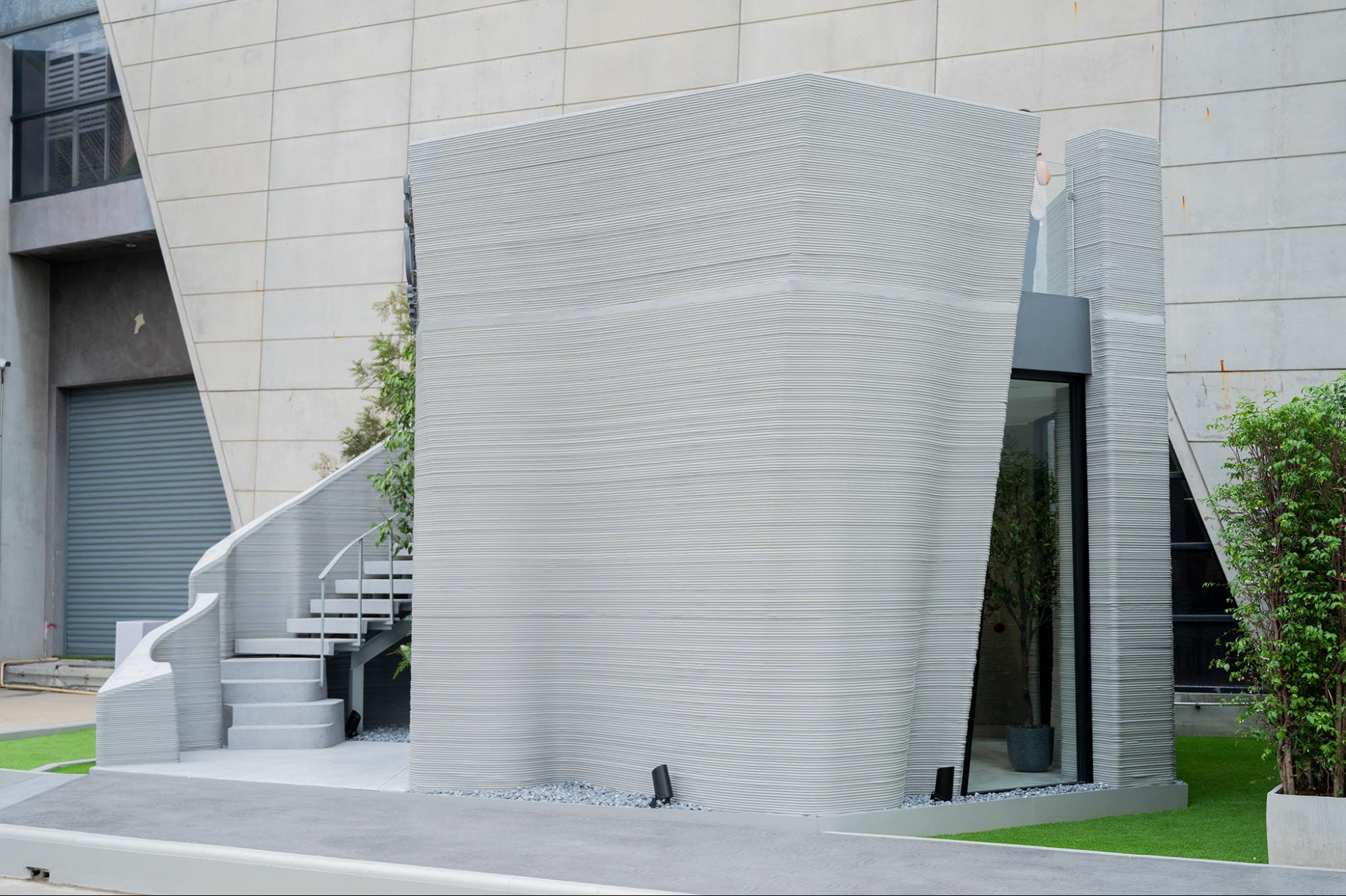
Efficient On-Site Construction Process
The construction process was divided into three main phases: site preparation, factory fabrication, and on-site installation. Site preparation, completed in 10 days, occurred simultaneously with module production, which reached 95% completion during this time. Fabrication of the six modules—including floors, 3D-printed walls, steel structures, and off-site finishing—was completed in 33 days. Once fabricated, the modules were transported 150 kilometers to the site, where installation took only 5.5 hours. Final on-site finishing was completed in 7 days, resulting in a total construction time of 41 days, with 65% of the work completed off-site.
When compared to traditional construction methods, the 3D-printed PPVC approach significantly reduced building time, cutting the schedule by 48% compared to brick-and-mortar construction and 54% compared to precast concrete, saving between 25 and 38 days.
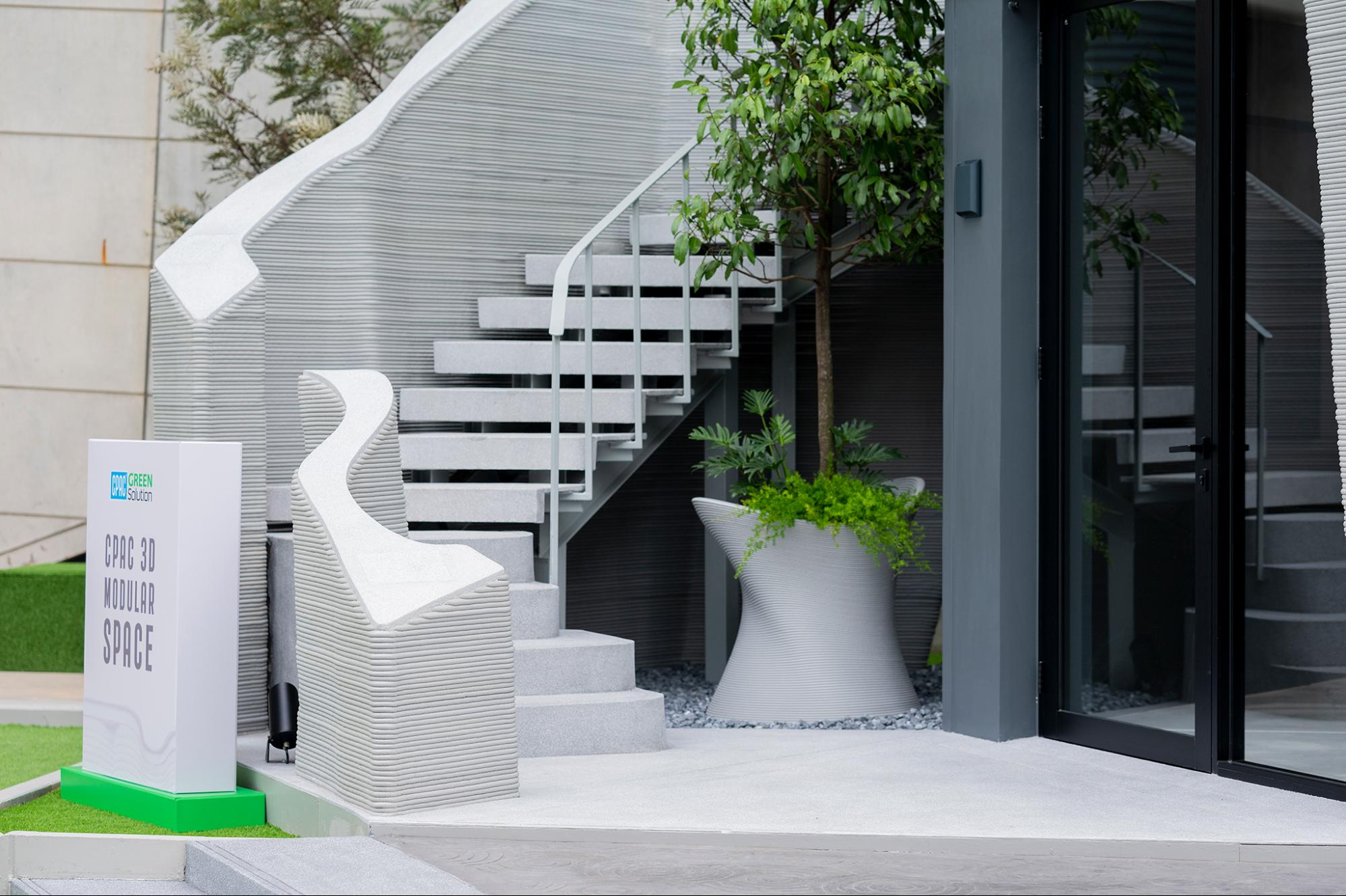
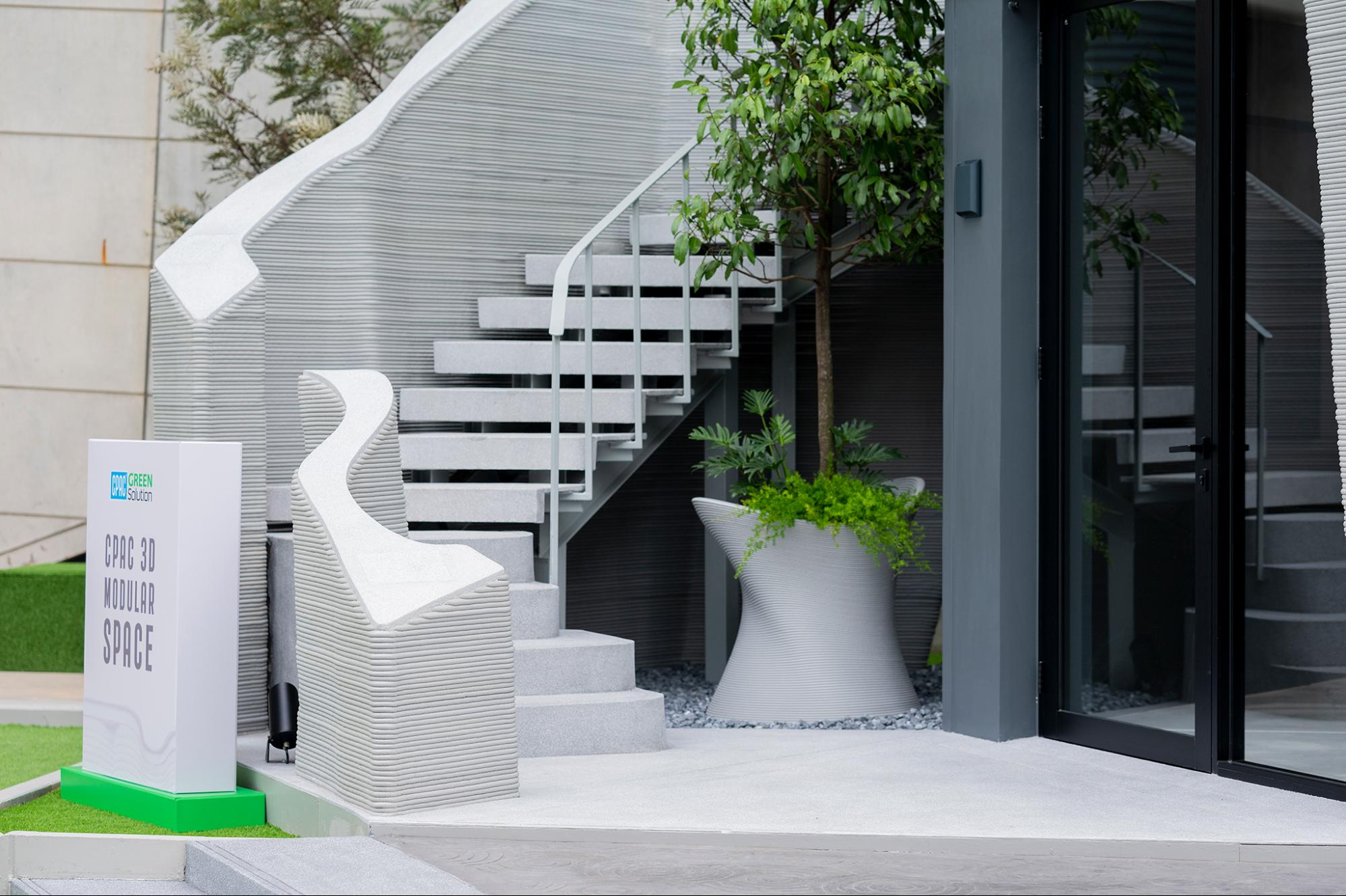
SCG Cement Co.,Ltd Encourages Industry Adoption of 3D Printing for a Sustainable Future
Thailand’s 3D-printed modular building project highlights the powerful role that low carbon materials and 3D printing can play in shaping the future of construction. SCG Cement Co.,Ltd as the driving force behind this initiative, encourages industry leaders, developers, and architects to consider the benefits of adopting similar methods in their projects. With climate change driving an urgent need for sustainable solutions, SCG Cement Co.,Ltd believes that combining 3D printing technology with low carbon materials offers a compelling path toward achieving global carbon reduction targets.
SCG Cement Co.,Ltd invites stakeholders to explore how these innovative approaches can contribute to sustainability efforts while also enhancing efficiency, reducing material waste, and producing resilient structures. By embracing low carbon mortar and 3D printing, the construction industry can make a significant impact on reducing emissions and minimizing environmental impact without compromising quality.
By committing to innovative, low-emission building solutions like those demonstrated in this project, we can collectively work towards a greener, more sustainable future for the next generation.
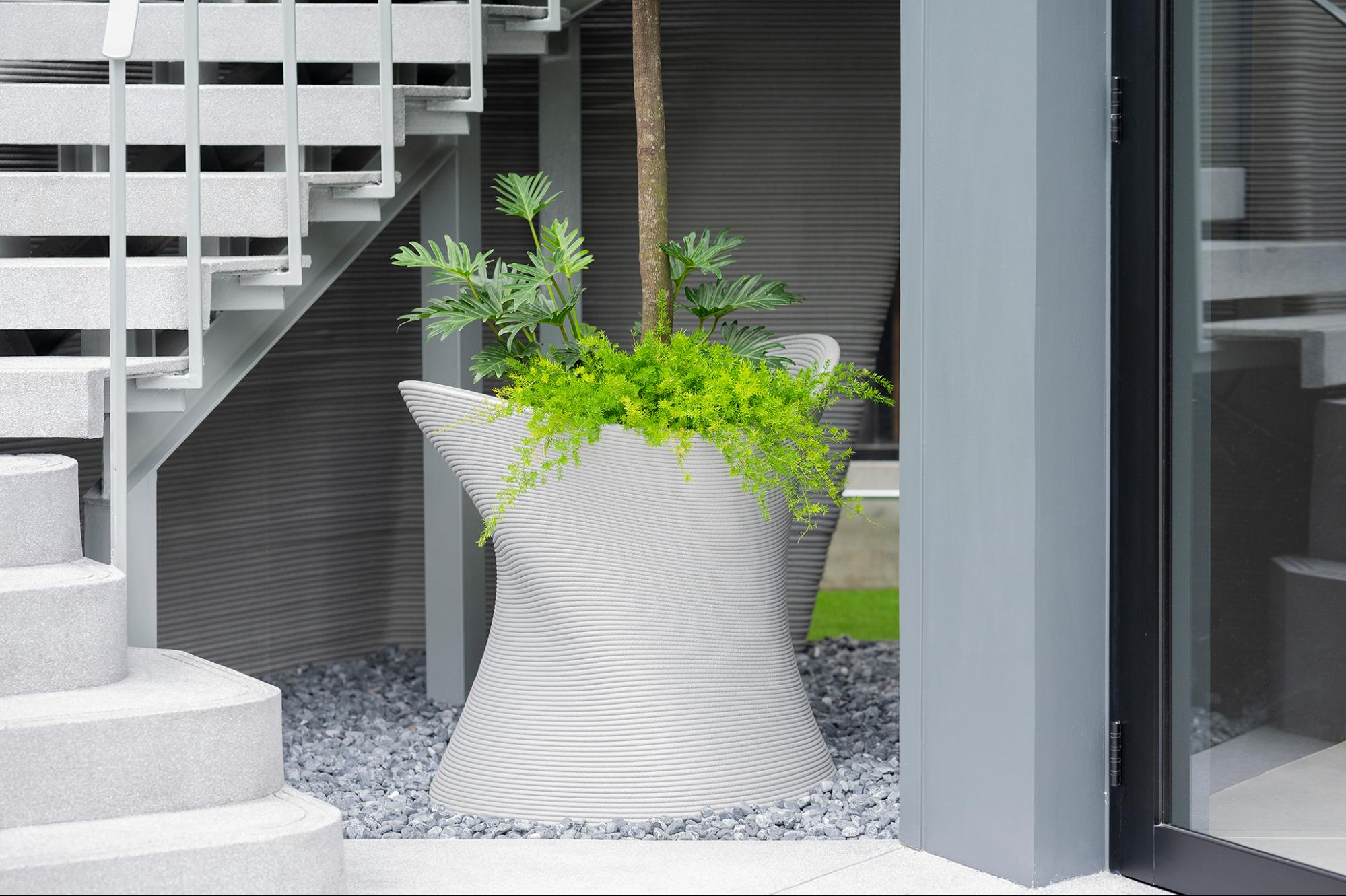
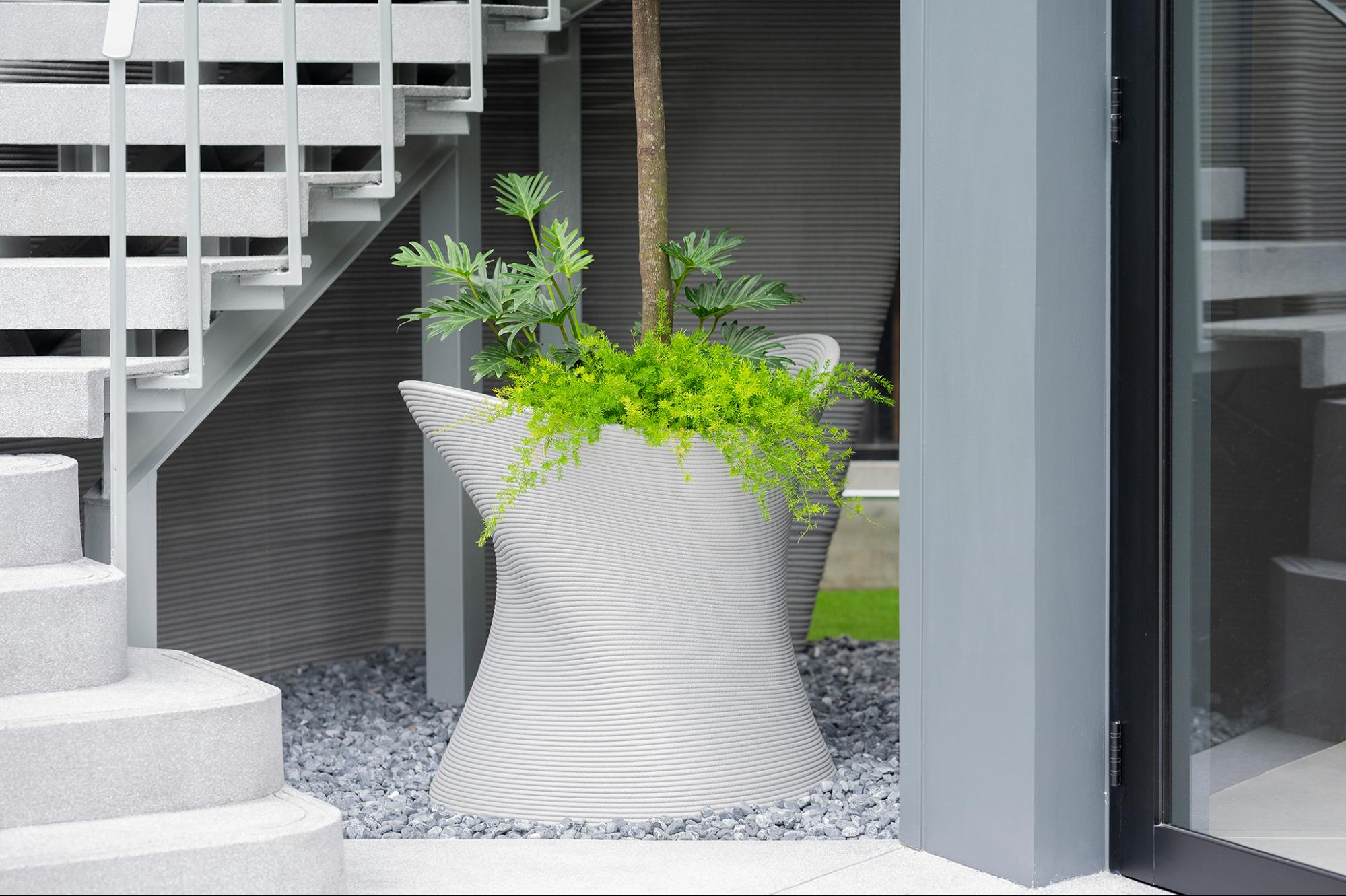
Access the Full Use Case
For those interested in a deeper dive into the technical aspects of this project, the complete use case is available upon request. You can contact (pattarut@scg.com). This document offers further insights into the challenges encountered during the design and production phases and provides a detailed look at the integration of biochar into the construction materials. It also covers logistical considerations, including module transportation and on-site assembly, which played a critical role in the success of this innovative initiative.
References
This project builds upon prior research and methodologies outlined in key academic works. Notable references include:
Jongvisuttisun, P., Chaiyapoom, P., Jiramarootapong, P., Meemuk, K., Snguanyat, C. (2024). The Second 3D-Printed Prefabricated Prefinished Volumetric Construction Building in Thailand: A New Sustainable and Efficient Approach for a Low-Rise Prefab Modular Building. In: Lowke, D., Freund, N., Böhler, D., Herding, F. (eds) Fourth RILEM International Conference on Concrete and Digital Fabrication. DC 2024. RILEM Bookseries, vol 53. Springer, Cham. https://doi.org/10.1007/978-3-031-70031-6_4