Vallourec, a leading French tube manufacturer, has successfully used wire arc additive manufacturing to create a downhole component that meets stringent American Petroleum Institute standards. The company’s commitment to WAAM signals a promising shift in the use of 3D printing technologies for the oil and gas industry.
Vallourec, which generates $3.4 billion in revenue and employs 17,000 people, has long been recognized for its expertise in seamless steel tubes for sectors such as energy and automotive. In a LinkedIn post, Vallourec’s Head of Additive Manufacturing, Olivier Tartar, highlighted the firm’s latest achievement: producing a downhole component using WAAM technology, which passed the demanding API 5C5:2017 CAL-IV standard for tubing and casing connections.
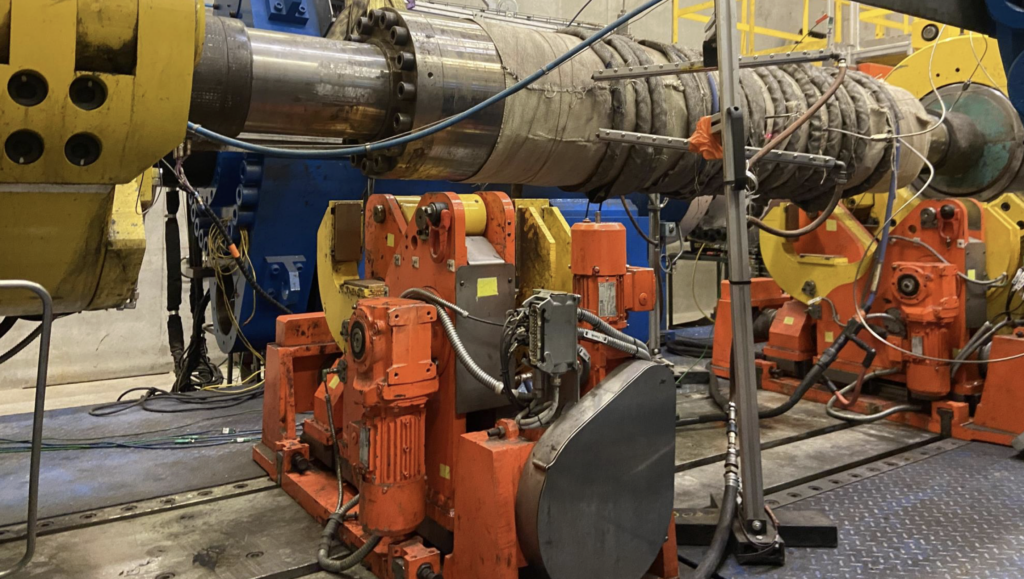
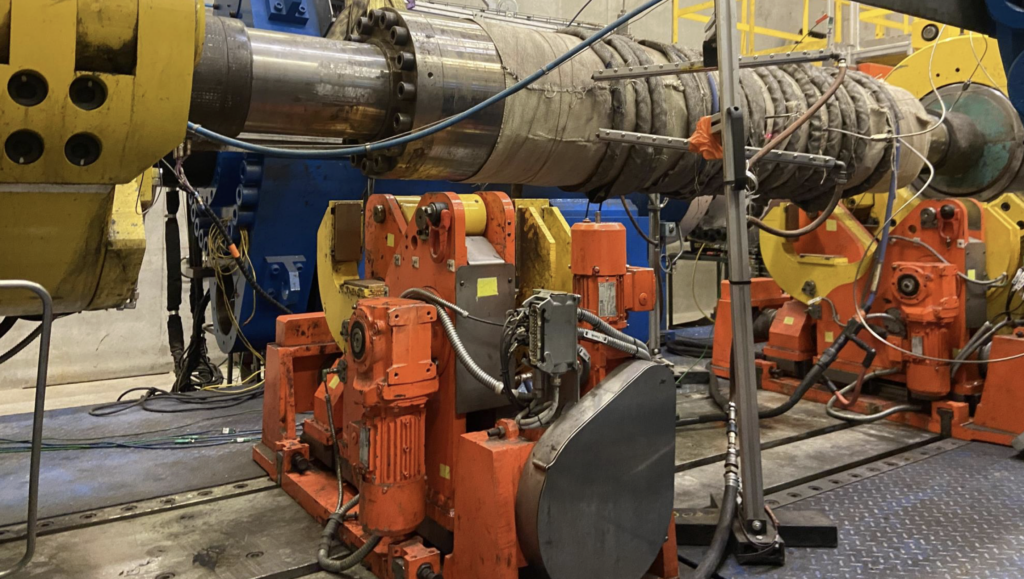
Despite initial hesitations within the industry, WAAM is gaining renewed attention for its speed and cost-effectiveness, particularly in the energy sector. Vallourec’s focus on refining this technology involves integrating robot arms and ultrasonic inspections in production cells, allowing the manufacture of large parts, up to 2 meters high and 1 meter in diameter. This capability is critical for industries that demand rapid, high-quality production.
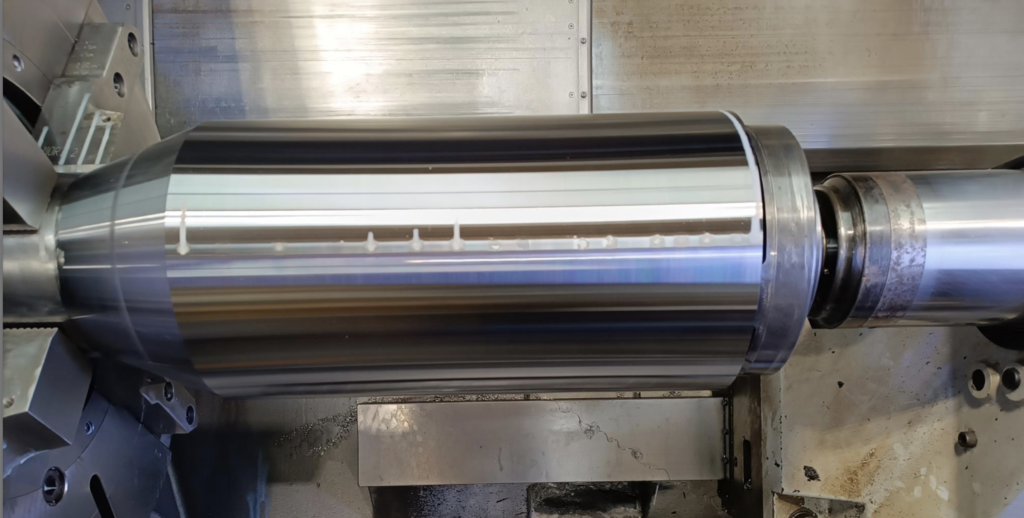
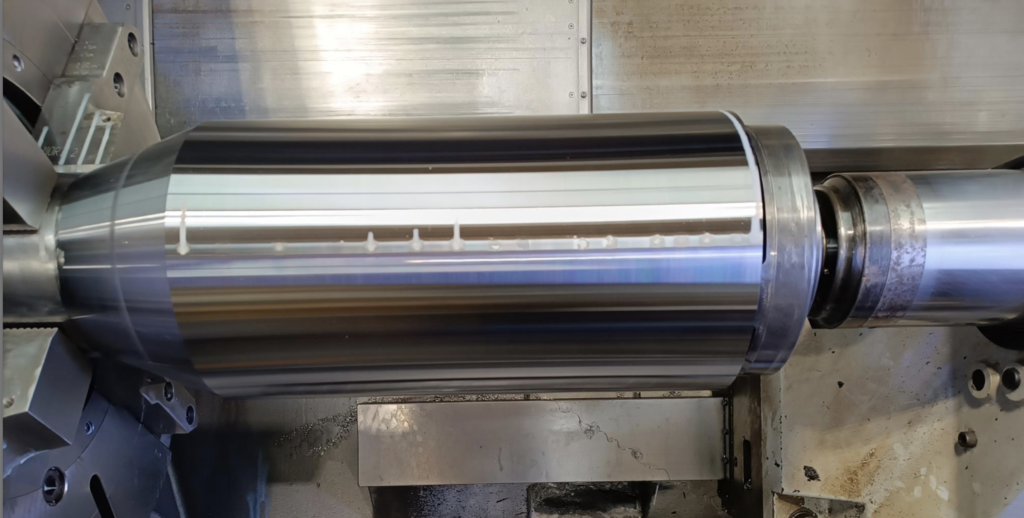
Innovations in WAAM Technology
WAAM technology has experienced ups and downs over the years. While it was initially embraced, its use dwindled due to challenges like post-processing and control limitations. However, Vallourec has refined the process by integrating robotic systems and advanced inspection tools, enabling the creation of high-performance components.
For example, Vallourec successfully produced a lifting plug for an oil platform in the Timor Sea, capable of withstanding a 100-ton load. This part was made at a fraction of the time and cost compared to the traditional forged alternative. Such advancements showcase the potential of WAAM to address urgent industry needs, such as reducing downtime in oil and gas exploration and production.
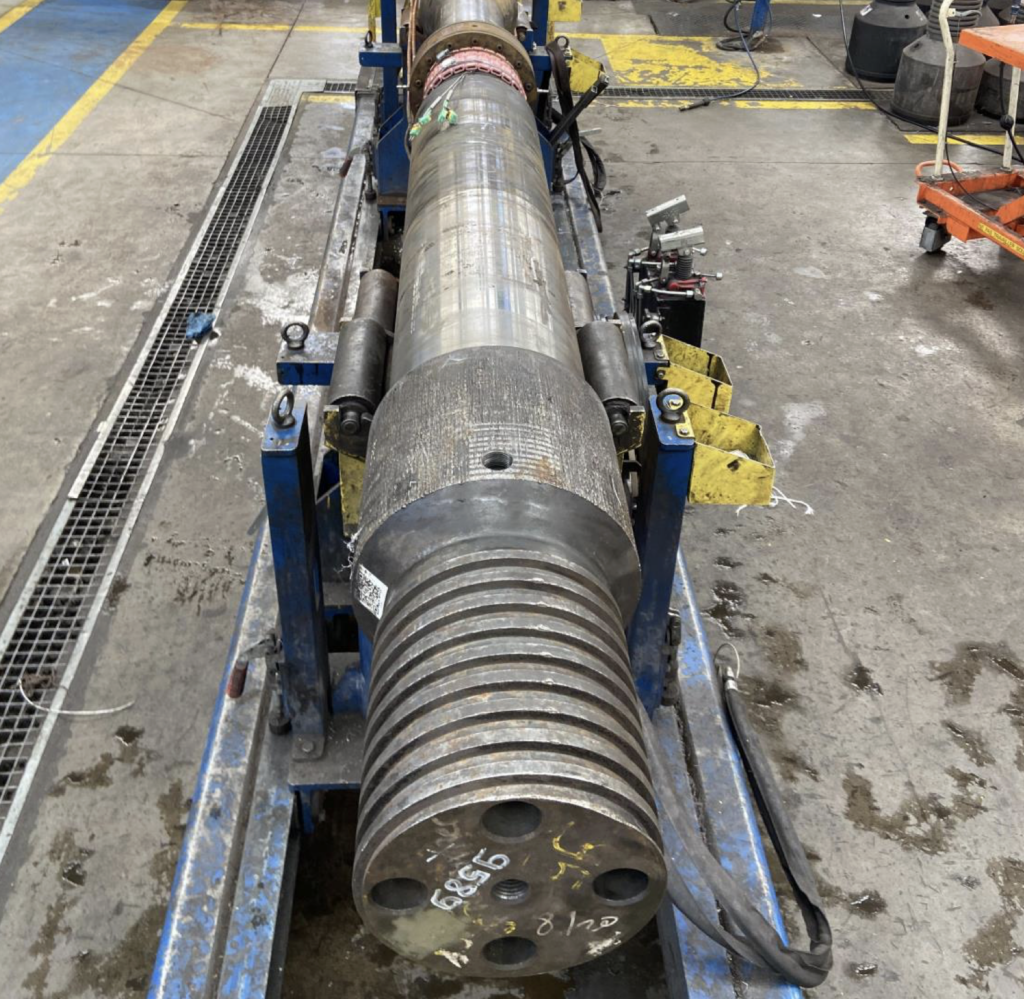
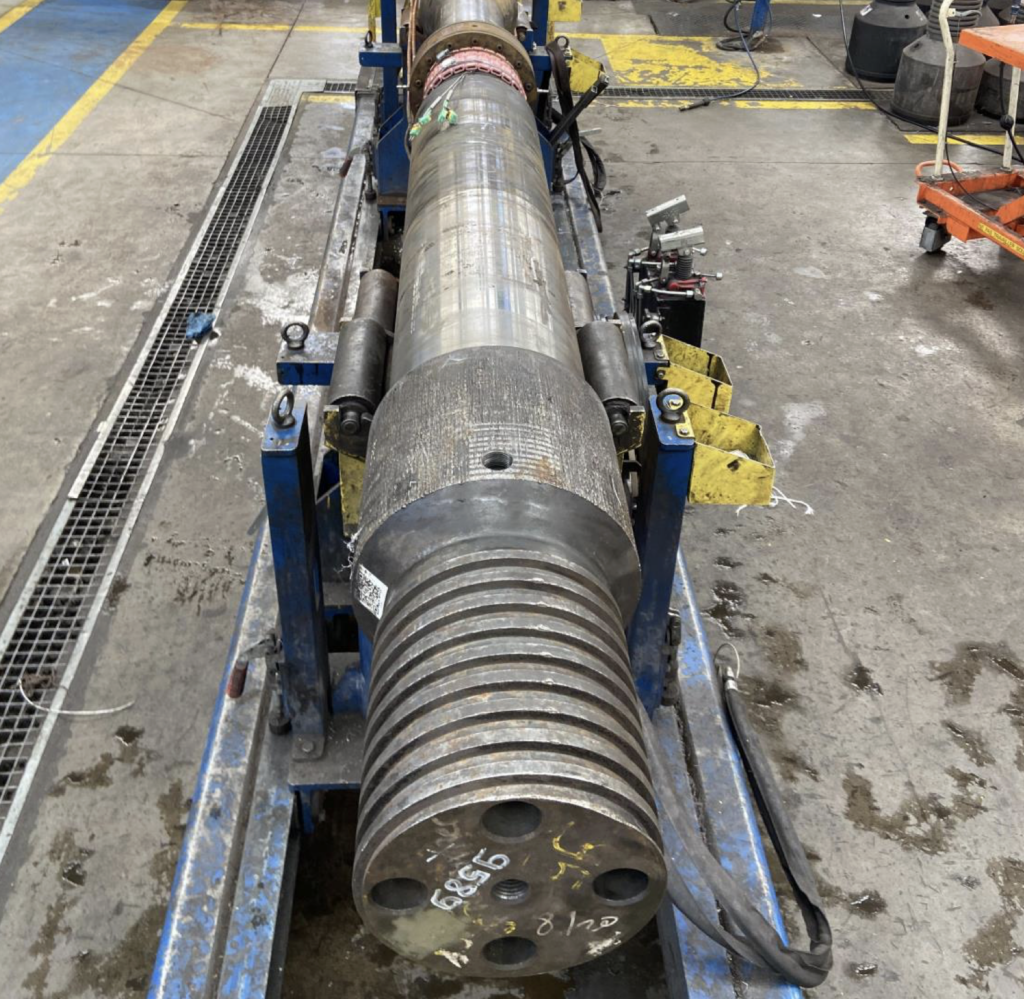
Meeting API Standards with 3D-Printed Components
The recent success of Vallourec’s WAAM-printed downhole component, which passed the rigorous API 5C5:2017 CAL-IV standard, marks a major milestone. The API standard ensures tubing and casing connections can endure high-pressure, high-temperature conditions commonly encountered in oil and gas operations. Vallourec tested a 9 5/8” cross-over tube under extreme conditions, applying both tension and compression, and subjected it to internal and external pressures of up to 1,000 bars and 600 bars, respectively.
Olivier Tartar emphasized that the success of this component demonstrates WAAM’s competitiveness with conventional manufacturing methods, including casting and forging. As Vallourec continues to refine the technology, the potential for widespread adoption in critical sectors becomes more apparent.
Source: 3dprint.com