On the floor of this year’s International Manufacturing Technology Show (IMTS), the theme for original equipment manufacturers (OEMs) in additive manufacturing (AM) seemed to be indirect production. What if, by 3D printing tooling, the technology could impact the production of millions of parts immediately indirectly rather than direct manufacturing of end parts in the future?
No one knows this strategy better than 3D Systems (NYSE: DDD), which was a key enabler to the birth and success of the invisible aligner market. There, the company’s stereolithography (SLA) machines are used to 3D print patient-specific thermoforming molds for millions of clear dental aligners annually.
Building upon that success is Patrick Dunne, Vice President of Advanced Application Development at 3D Systems Corporation. We sat down with Dunne to discuss the company’s latest product, QuickCast Air, and how it’s poised to advance the investment casting industry.
The Genesis of QuickCast Air
Investment casting, a process thousands of years old, has seen incremental advancements over the centuries. However, the introduction of QuickCast Air marks a leap forward. Dunne explains that the innovation was born out of a need to make 3D printing more cost-competitive with traditional manufacturing methods.
“This is one of the first examples of an additive manufacturing workflow that is cost-competitive with traditional manufacturing,” Dunne said. “Historically, 3D printing has always presented a long list of value propositions—it’s faster, there’s no tooling, and there’s flexibility to change your design on the fly. But there’s always been that question about part-to-part, pound-for-pound economics.”
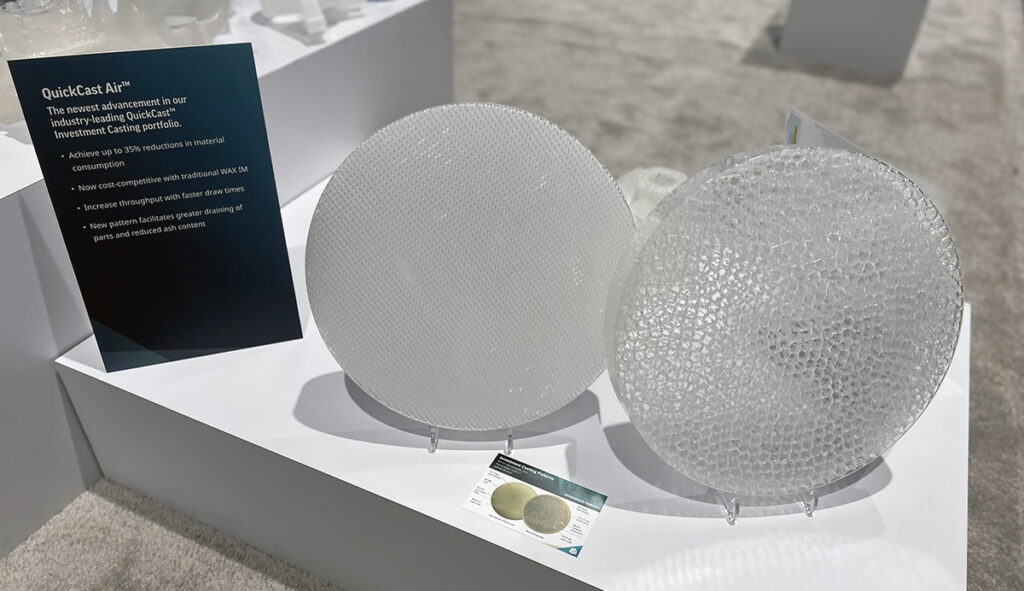
3D printed QuickCast Air parts from 3D Systems.
Dunne pointed out that foundries typically balk at the high cost of 3D printing materials compared to traditional materials. “When they ask a 3D printing company, ‘How much is your material?’ it’s typically $90 to $120 per kilogram, whereas they pay about $10 per kilogram for injection molding wax. The meeting often just comes to a grinding halt,” he noted.
Flipping the Script on Material Efficiency
To address this cost disparity, 3D Systems focused on leveraging the inherent strengths of 3D printing—namely, its ability to create complex geometries with minimal material usage. “We realized 3D printing is really good at making complex shapes. So, why don’t we turn that inside out and make the patterns hyper-efficient?” Dunne suggested.
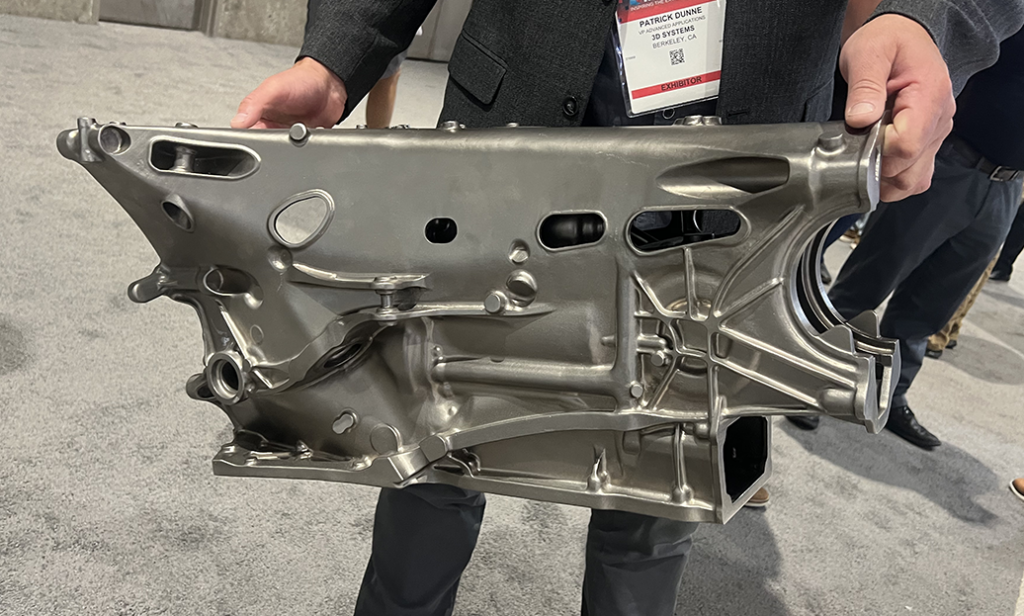
An investment casted metal part for an F1 team made using a 3D printed QuickCast Air pattern.
Enter QuickCast Air, a solution that allows for the creation of casting patterns that are 95% air and only 5% plastic. “Even though the material is ten times more expensive, using 95% air means the actual material cost in the part is about $5—half the price of wax,” Dunne explained. “We bring all the benefits of 3D printing and now check that final box in the list, which is cost competitiveness.”
This innovation is poised to open doors in the traditionally conservative foundry industry. By significantly reducing material consumption and costs, QuickCast Air makes 3D printing a viable alternative for large-scale investment casting applications.
Hybridizing Traditional and Digital Manufacturing
Dunne emphasized that QuickCast Air represents a hybrid approach, merging the best of traditional manufacturing with state-of-the-art digital technologies. “You’re taking an old traditional manufacturing process that gives you access to almost infinite alloys in a very economical workflow, which is investment casting, and you are merging it with state-of-the-art digital technologies, which is 3D printing,” he said.
This hybridization allows for practical outcomes in extensive applications. “We bring the best of 3D printing and the best of traditional manufacturing together in these indirect workflows,” Dunne added.
Real-World Applications and Customer Success
QuickCast Air is already making waves in industries where high performance and precision are paramount. While Dunne couldn’t disclose specific customer names, he mentioned that the technology is being used extensively in “orbital lift.”
“They value high performance, which they get with 3D printing—the complex shapes, liquid oxygen, methane manifolds, convergent and divergent nozzles, among other applications. There’s a ton of casting in these components,” he said.
One tangible example is a titanium casting for a Formula One car, produced using a QuickCast pattern. “That’s an investment casting pattern created using QuickCast, and that’s a titanium casting from that pattern,” Dunne noted, showcasing the versatility and precision of the technology.
Expanding Industrial Applications
Beyond investment casting, 3D Systems is seeing rapid industrialization in other sectors. “The other area we’re seeing rapid industrialization is semiconductors,” Dunne said. “The equipment used to make microchips—big machines where they’re moving wafers and imaging on wafers—needs to be temperature-controlled to decimal points.”
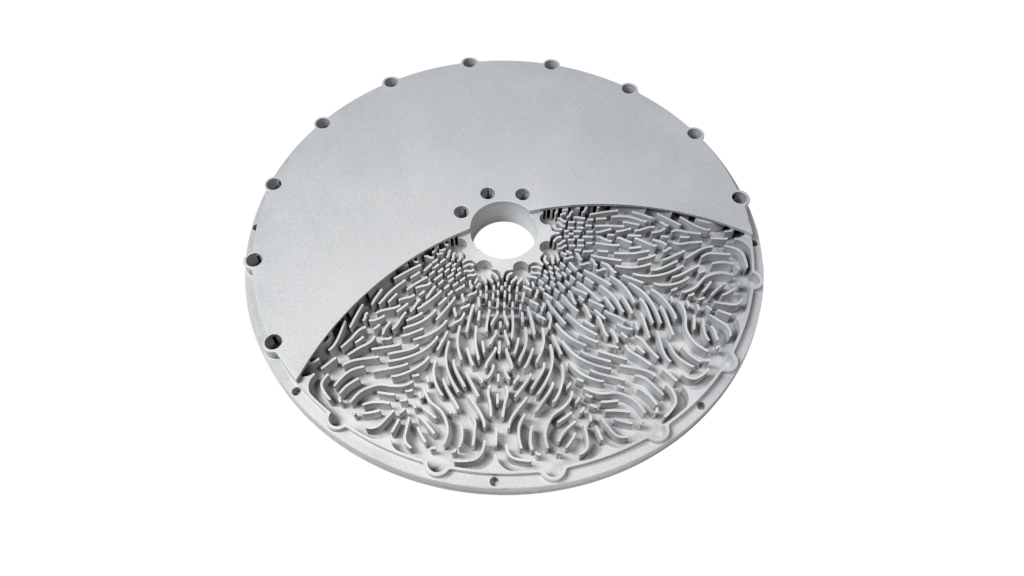
Better thermal management of wafer tables can simultaneously improve semiconductor equipment accuracy by 1–2 nm, as well as speed and throughput. (Image courtesy of 3D Systems)
AM enables designers to create sub-components that are lightweight, have low inertia, and are thermally controlled using advanced cooling techniques. “We’re seeing extensive application in that space,” he added. The immense opportunity for this vertical is discussed in greater detail in the “3D Printing for Semiconductors: Market Opportunity Brief” from Additive Manufacturing Research, which estimates that 3D printing in the semiconductor market will generate $160M of market activity in 2024, with the potential to grow to $1.4 billion in 2032.
In aerospace and defense, including everything from submarines to aircraft, AM is becoming a standard mode of production. “It’s becoming a standard mode of manufacturing, which, in my opinion, is the very definition of the industrialization of a technology,” Dunne stated.
Innovations in Metal Printing and Tooling
Dunne highlighted the company’s advancements in direct metal printing, particularly with challenging materials like tungsten. “Making a tungsten part like this using traditional methods is extremely difficult,” he explained, showcasing a heavy, complex nuclear collimator. “You can’t cast it because of its high temperature, and it’s very hard to machine because it’s super hard, wear-resistant, and quite brittle.”
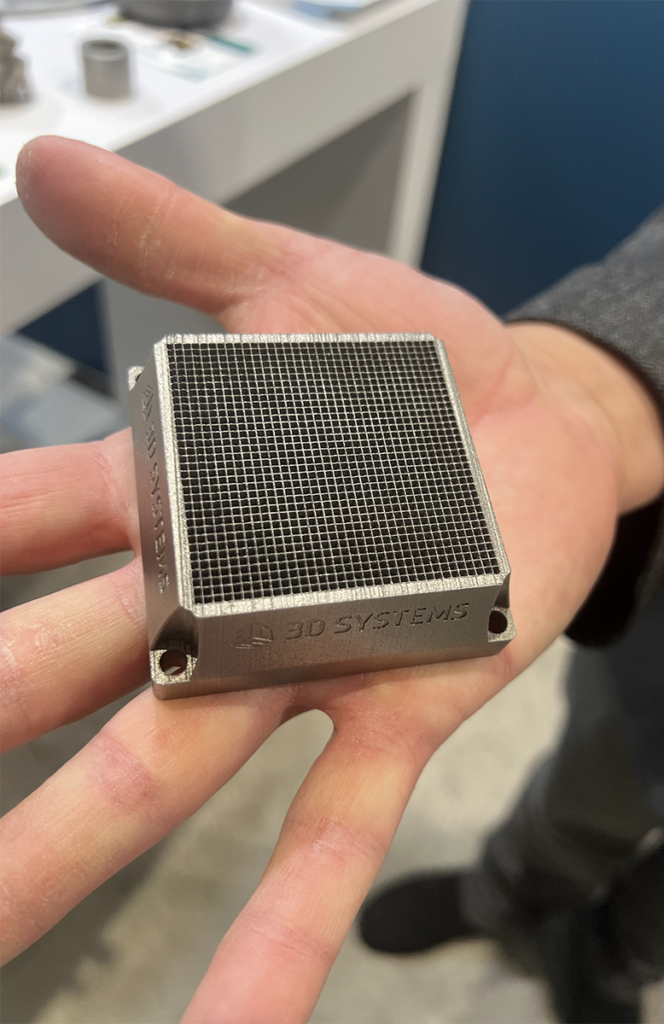
A 3D printed nuclear collimator made from Tungsten using 3D Systems’ Direct Metal Printing laser powder bed fusion process.
Using concentrated fiber lasers, 3D Systems can create exotic shapes in tungsten, opening new possibilities in the nuclear and semiconductor industries. “Designers can now process an old material like tungsten with a new technology like powder bed fusion, enabling new capabilities,” Dunne said.
Indirect Workflows and the Future of Manufacturing
Dunne stressed the importance of indirect workflows in AM, where 3D printing is combined with traditional manufacturing processes to produce end-use parts. “People underappreciate that 90-something percent of all production-grade 3D printed objects in the world are indirect,” he noted.
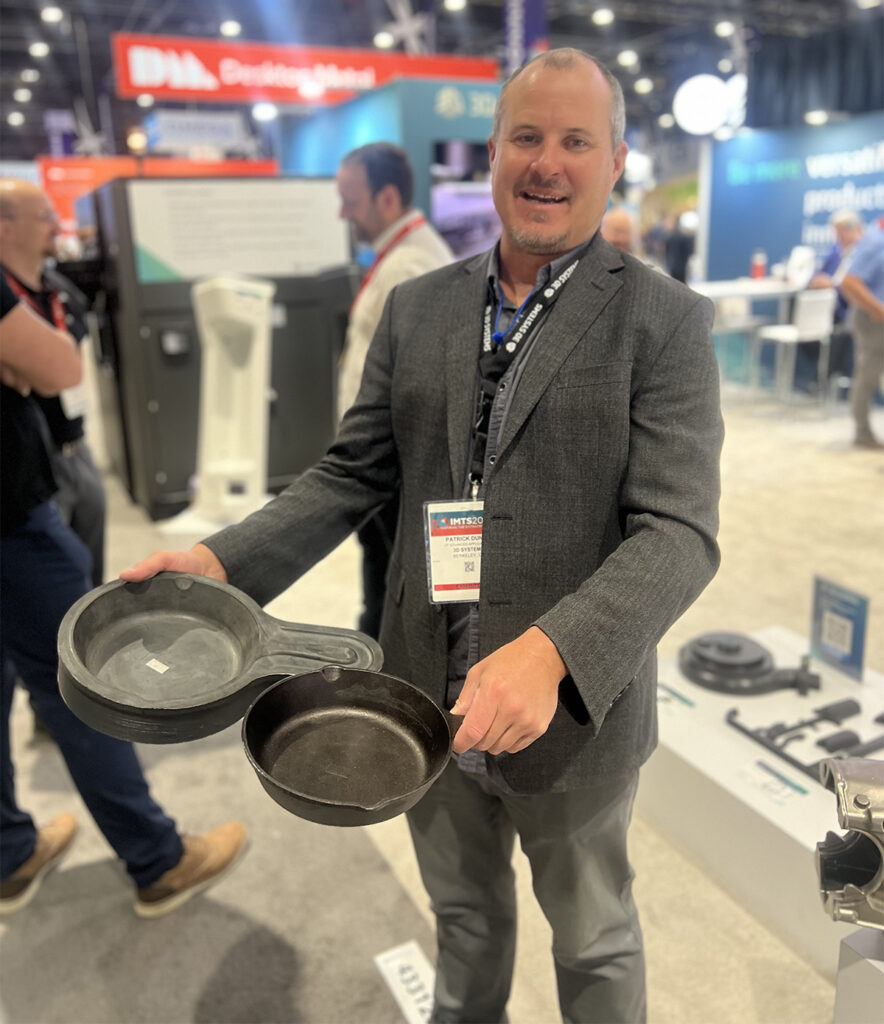
Dunne holding a mold 3D printed using the Titan pellet extruder system and used to cast metal pans.
He cited examples like clear orthodontic aligners, which use mass-customized, single-use disposable thermoforming tools, and the extensive use of 3D printing in investment casting for jewelry. “You’re combining the best of 3D printing with the best of traditional manufacturing to give you parts that are ready to go,” he said.
Addressing the use of 3D printing in prototyping and bridge production, Dunne highlighted how companies can utilize these technologies to accelerate product development. “Companies may need to make 500 units to go out into the market and do market feedback, research, testing, comfort, wearability—all of the above,” he explained. “It’s hard to simulate; you have to actually build it and test it.”
While these are not final production versions, AM allows for rapid iteration and testing before investing in mass production tooling. “We do see some of that in consumer automotive,” Dunne added. “As soon as the injection molding tool is redone, they will substitute in the injection molding for the 3D printing process and bring the economics around.”
A New Generation Embracing Additive Manufacturing
Dunne observed that a new generation of engineers is entering the workforce, one that has grown up with 3D printing as a default manufacturing option. “We’re seeing a lot of that right now—the new generation coming into the industrial space is operating on the assumption that additive is the way to solve most problems,” he said. “Which is good for us.”
This shift in mindset is accelerating the adoption of AM across various industries, further solidifying its role in modern production workflows.
Looking Ahead
With QuickCast Air, 3D Systems is not just introducing a new product but is pushing the boundaries of what’s possible in manufacturing. By addressing the critical cost barriers and leveraging the strengths of both traditional and AM, the company is poised to make significant inroads into industries that have been historically resistant to change.
As the investment casting market continues to grow—projected to reach $33.9 billion by the end of 2034—the introduction of cost-effective, efficient alternatives like QuickCast Air positions 3D Systems at the forefront of industry disruption.
Subscribe to Our Email Newsletter
Stay up-to-date on all the latest news from the 3D printing industry and receive information and offers from third party vendors.