Simpliforge Creations and IIT Hyderabad have completed a 3D printed military bunker at 11,000 feet in Leh, India. The protective bunker was constructed in collaboration with the Indian Army under Project PRABAL. This marks the first on-site 3D printed military structure built in high-altitude, low-oxygen conditions using locally sourced materials.
The structure was printed in 14 hours using Simpliforge’s robotic 3D printer, which was deployed and commissioned in under 24 hours. CEO Dhruv Gandhi noted several challenges: “Reduced oxygen levels impaired power efficiency and human performance. Low humidity and high UV radiation impacted material integrity—but our systems delivered a robust structure in just 5 days.”
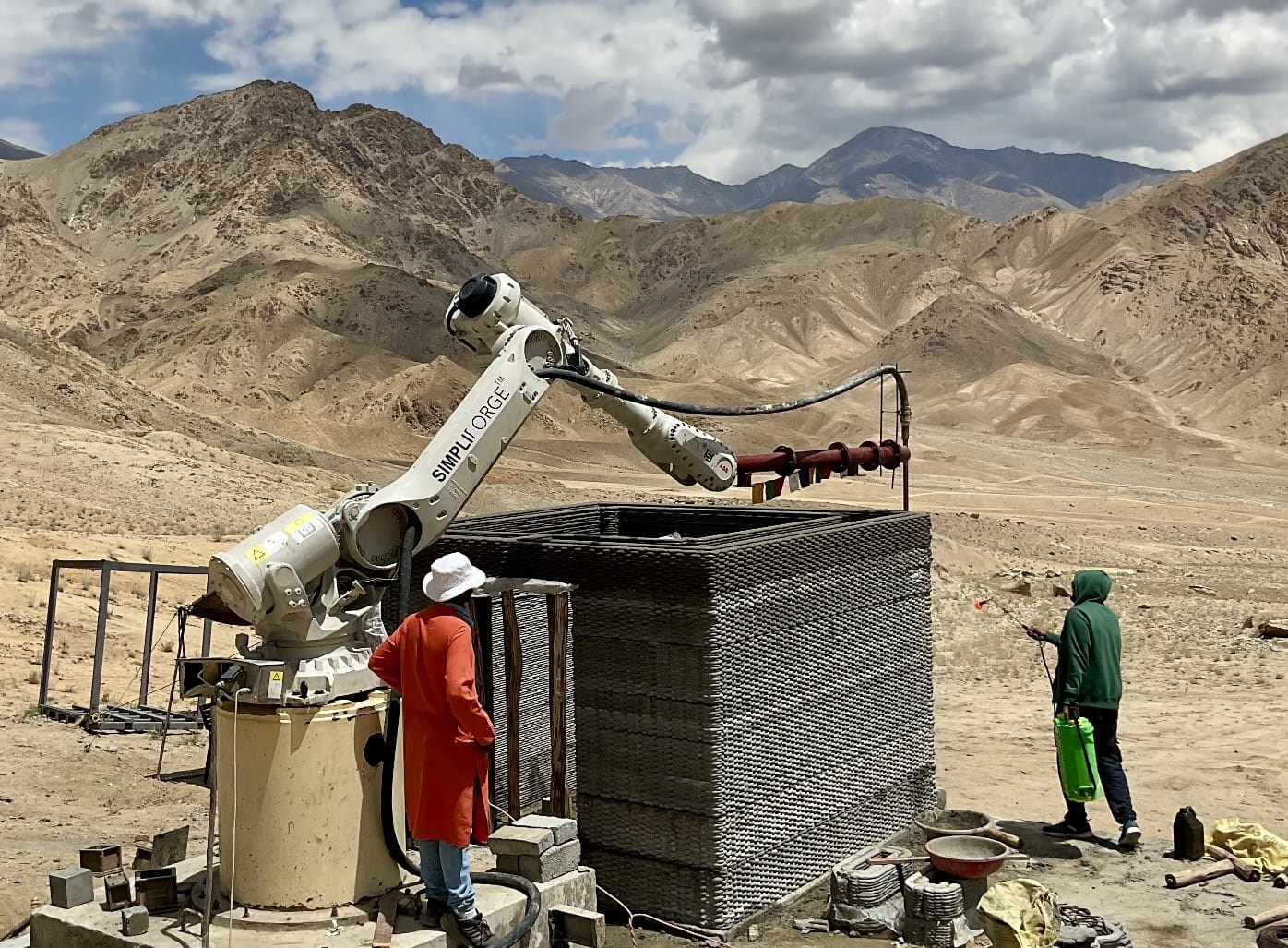
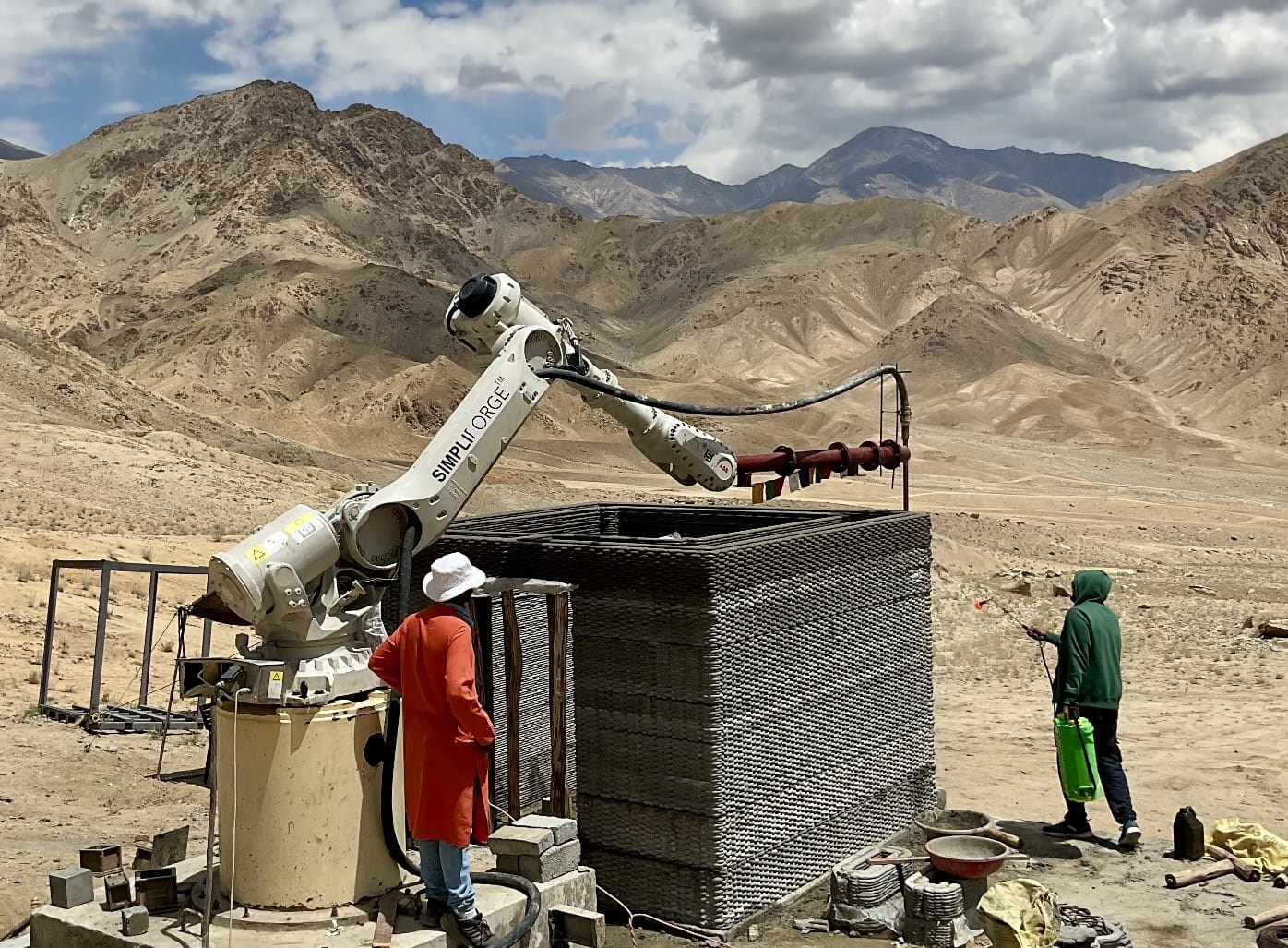
Material science played a crucial role in the project’s success. Prof. K.V.L. Subramaniam of IIT-Hyderabad explained: “Operating at high altitudes with thermal extremes required specially engineered concrete. Our team rigorously tested and optimized a mix suited to local aggregates and environmental stresses. This innovation was key to ensuring structural strength and durability.”
The project team included PhD scholar Arun Krishnan, who stated, “Project PRABAL began during my M.Tech journey. Previous attempts to bring 3D construction to Ladakh faltered due to harsh conditions. It was the synergy between IIT Hyderabad and Simpliforge that finally overcame these barriers. We’ve proven that homegrown technology can thrive even in the toughest environments.”
Hari Krishna Jeedipalli, MD of Simpliforge, connected this achievement to potential future applications: “From India’s first 3D printed bridge to the Army’s medical facility, each project has advanced the frontier. This Ladakh bunker is more than a defense milestone—it’s validation for extra-terrestrial applications. We see this as a stepping stone toward space construction on the Moon and Mars.”
The project demonstrates how 3D printing technology can provide rapid infrastructure solutions in extreme environments. Using local materials and completing the structure in days rather than weeks highlights potential applications for remote construction challenges.