PanOptimization and its product, PanX, is a potentially groundbreaking additive simulation tool that can quickly simulate large, complex files on regular PCs. Reportedly more accurate than other alternatives, it also helps predict build failures and addresses issues such as trapped powder. The firm is now partnering with the affordable powder bed fusion maker, Xact Metal.
“We are pleased to partner with PanOptimization to bring cutting-edge simulation and optimization into the additive manufacturing industry. “In our drive to lower the price of additive manufacturing metal powder-bed fusion systems, we have used PanX to help us improve the performance of our systems, understand the behavior of the metals that we work with, and optimize the parts that we are printing to achieve the geometric performance that we require.We ourselves have seen the value that PanOptimation’s software provides and want to bring this benefit to our manufacturing customers, such as those in the injection molding industry, supported through our sales network of over 26 partners around the world,” said Xact Metal CEO Juan Mario Gomez.
“We’re excited to begin our partnership with Xact Meta. It is a logical next step in our strategy to integrate our PanX software product line with all major machine OEMs, and an opportunity for us to go beyond our aerospace and defense user-base and expand into the broader industry of affordable metal additive manufacturing,” stated PanOptimization CEO Pan Michaleris.
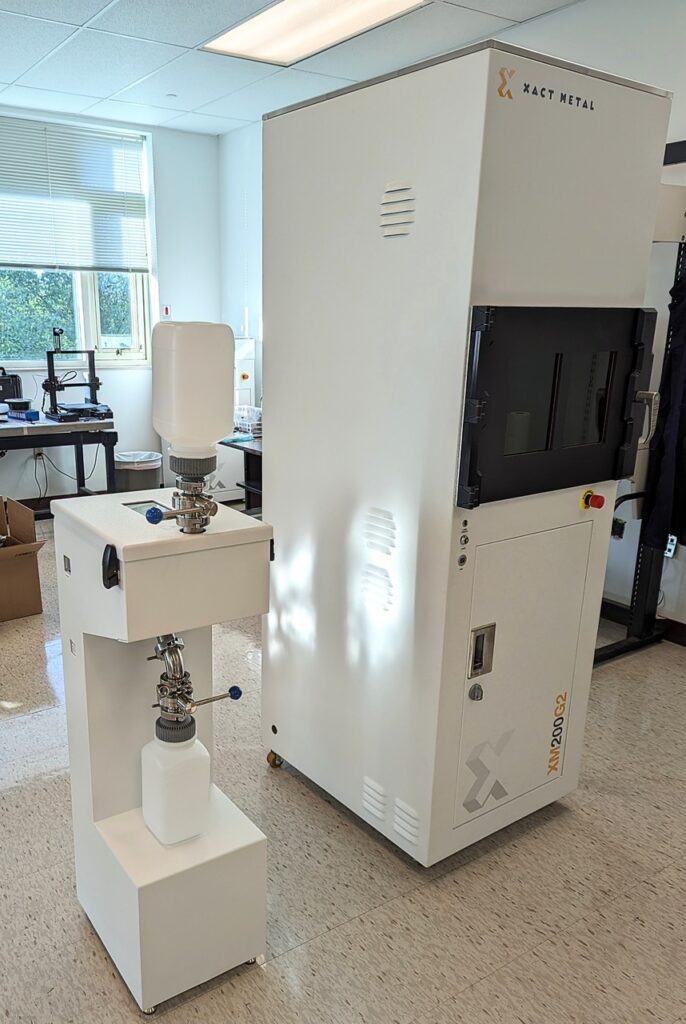
Xact Metal’s new powder handling machine next to the XM200G metal 3D printer. Image courtesy of Xact Metal.
Simulation is often too costly or time-consuming for more routine print jobs. It’s encouraging to see that these low-cost machines can also utilize the software, allowing it to be used on a daily basis. PanX claims its “unique multi-grid modeling approach for thermomechanical simulation achieves superior accuracy with runtimes between 100x faster and, in some cases, infinitely faster than traditional finite element analysis (FEA) models.” This impressive claim could help Xact Metal users improve settings, produce better parts, and experience fewer failed builds. Issues such as recoated bumps and cracking in models remain significant problems. These problems are also costly. If you amortize a printer over three years with 600 build days in that period, missing just one day is expensive, creating a clear quantifiable loss. You don’t need to save more than a handful of builds to make FEA a very worthwhile investment. At the same time, much of powder bed work can resemble water witching, where tradition, norms, and skill combine into a practical art form. A surprising amount of time is spent adjusting settings and achieving success by the fifth attempt. FEA software can assist here as well, helping to satisfy customers more quickly, keep machines running, and improve overall productivity.
The intersection of software and machinery is where much of the current innovation is happening. On one hand, there’s exciting progress in improving machine settings. Many firms have discovered hacks, code, practices, and files that provide them with a competitive advantage. As more people purchase machines, extracting maximum value from a specific setup becomes increasingly important. Simultaneously, the growing installed base of machines is driving more interest and investment in optimization.
Previously, vendors controlled the firmware, G-code, and settings, but now high-end services are customizing these extensively. At the same time, a wave of software startups is competing to offer optimization solutions. The existing installed base of 3D printers has been increasingly customized and optimized for specific purposes. Metal powder bed fusion machines were once either loaded with extensive settings for researchers focused on characterizing materials like Inconel 718, or designed to print a wide variety of geometries for service bureaus. Now, new customers often focus on a single material and may print only one geometry (or a family of similar geometries) throughout the machine’s lifetime. This shift is changing the way operators and OEMs approach machine use. Custom machines with highly optimized code are becoming more prominent.
The challenge now is how to achieve the ideal state of perfect production for that one part. PanX aims to play a role in this transformation, and Xact Metal could be the company that supplies many production machines optimized for specific tasks or parts. I’m excited about this partnership and hope to see fully functional FEA tools widely integrated across machines, shifting the industry from guesswork to a more precise process.
Subscribe to Our Email Newsletter
Stay up-to-date on all the latest news from the 3D printing industry and receive information and offers from third party vendors.