In today’s 3D Printing News Briefs, America Makes has put out its latest Project Call, and Nikon SLM Solutions is adding Dyndrite LPBF Pro software to its product offering. Moving on, AddUp’s strategic partner Acuity Surgical Devices received FDA 510(k) clearance for its 3D printed Ventris Interbody Fusion System. Finally, an agency is teaching disabled people in Connecticut and New York to use technology like 3D printing to make assistive solutions for themselves and their peers.
America Makes Announces $5 Million QTIME Project Call
America Makes and the National Center for Defense Manufacturing and Machining (NCDMM) have announced their latest project call, QTIME, or Quality Test and Inspection Methods Expediency. Funded by the Office of the Under Secretary of Defense, Manufacturing Technology Office (OSD ManTech), this project call is worth $5 million, and is all about non-destructive inspection (NDI) techniques for AM processes, specifically directed energy deposition (DED) and laser powder bed fusion (LPBF). The focus of QTIME is basically the most mature, near-commercial NDI technologies, both in-situ and ex-situ, for inspecting large and complex 3D printed parts. Up to five awards are anticipated to come out of this project call. The QTIME request for proposal (RFP) is divided into three topic areas: Rapid, Cost-effective Methods for Non-destructive Inspection of Large AM Parts; Rapid, Cost-effective Methods for Inspection & Qualification of Complex AM Parts; and Industry Transition Team (ITT). At the onset, proposed projects should apply to Technology Readiness Level 4-7 and Manufacturing Readiness Level 4-7. Questions about the scope or approach are due by May 15, 2025, while the membership eligibility deadline is June 17, 2025. The deadline for submission is 5 pm ET, June 30, 2025, and the awards announcement should be on July 30, 2025.
“Industry and government stakeholders have clearly identified the need for trusted, efficient inspection techniques to support additive manufacturing growth. The QTIME project call is an important first step, bringing together a diverse group of stakeholders and innovators to address both in-situ and ex-situ monitoring and inspection challenges inherent to AM,” explained Ben DiMarco, Technology Transition Director at America Makes. “QTIME focuses not just on developing new methods, but validating and transitioning mature technologies that agencies like the DoD, FAA, and NASA can trust—driving widespread adoption across the U.S. supply base.”
Dyndrite LPBF Pro Integrated into Nikon SLM Solutions Product Catalog
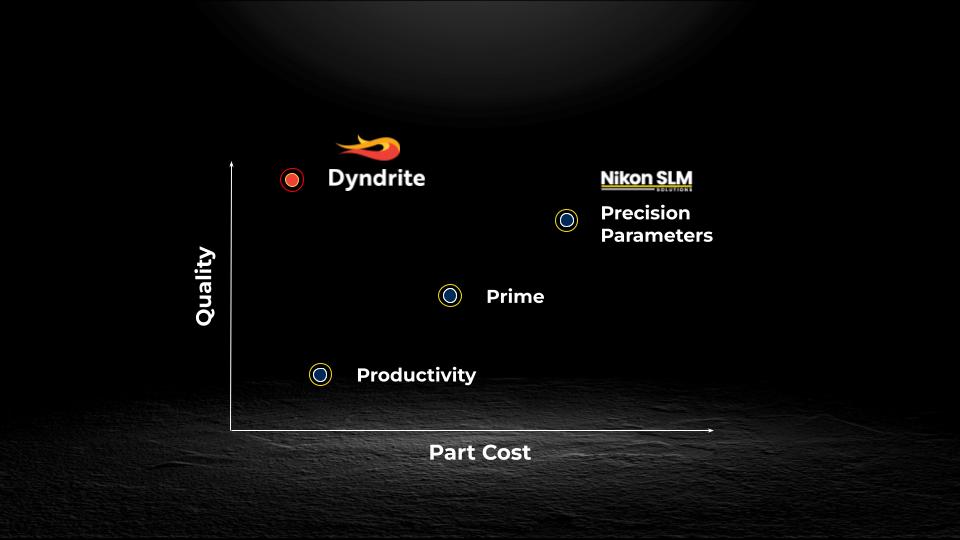
Dyndrite LPBF Pro eliminates the trade-offs between productivity, prime, and precision parameters. With Dyndrite, there’s no need to compromise—you can achieve high quality and lower part costs by applying them all simultaneously.
Additive manufacturing software company Dyndrite and metal AM solutions provider Nikon SLM Solutions announced the integration of Dyndrite LPBF Pro into the Nikon SLM Solutions offering, which will give metal 3D printing users a next-gen solution for printing support-free parts, speeding up build preparation, simplifying complex print workflows, and increasing production throughput. The software offers manufacturers an advanced GPU-accelerated software solution built for LPBF. Users have more control over their AM process, with automated scripting, improved part quality, scalable processing, and streamlined workflows; plus, they can maximize their Nikon SLM Solutions hardware investment. Dyndrite LPBF Pro has spent the past year undergoing a major evaluation process across all of Nikon SLM Solutions’ core machines, and the software’s performance was tested under real-world customer conditions, with multi-laser configurations and complex geometries. So now, Dyndrite is the first third-party software in over two decades to be given this level of support.
“Dyndrite has surpassed our expectations by unlocking new levels of performance for our customers. At Nikon SLM Solutions, we are always seeking innovative ways to help our users accelerate production and stay ahead of the competition,” said Charlie Grace, Chief Commercial Officer at Nikon SLM Solutions. “With the addition of Dyndrite LPBF Pro to our solution stack, we’re making high-performance metal additive manufacturing even more accessible, automated, and ready for industrial-scale deployment.”
To showcase their new integration, Dyndrite and Nikon SLM Solutions will host a joint commercial and hands-on workshop at the new Nikon AM Synergy facility in Long Beach this Tuesday, May 13th.
FDA 510(k) Clearance Granted to Acuity’s Ventris Interbody Fusion System
AddUp Inc. announced that its strategic partner Acuity Surgical Devices LLC received FDA 510(k) clearance (K243386) for its Ventris Interbody Fusion System, 3D printed on the FormUp 350 LPBF system. Established in 2013, Acuity is a leading medical device manufacturer based out of Irving, Texas, specializing in spinal surgery solutions with its state-of-the-art implant systems. Ventris is an advanced spinal implant device that’s designed to streamline clinical workflows and improve surgical outcomes with its increased surface area for better osteointegration and enhanced anatomical compatibility via lordosis options. Receiving 510(k) clearance shows that the Ventris system meets all the necessary safety and effectiveness standards, and a large part of this is due to the fact that Acuity now uses AddUp’s FormUp 350 platform. The LPBF system offers strong process control, high-resolution part production, repeatable part quality, and a unique modular architecture for safe, efficient powder management. This allows Acuity, and other medical device manufacturers, the ability to push the boundaries of implant geometry without compromising on regulatory compliance.
“This clearance represents a significant validation of our technology. We’re proud to support Acuity Surgical in bringing advanced, FDA-cleared spinal implants to market using the FormUp 350 platform. It’s a powerful example of how additive manufacturing is shaping the future of medical innovation,” said AddUp’s Deputy CEO Nick Estock.
Individuals with Disabilities in Product & Technology Development
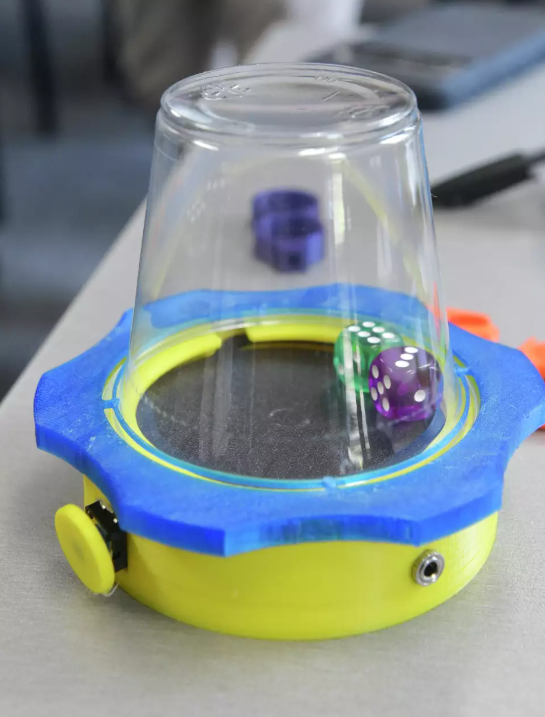
A device that rolls dice was created by Ability Beyond’s new training program called TIP Squad (Technology Innovations for Peers) that gives young adults with disabilities the opportunity to create solutions for peers, using 3D printers and other technology to design and build adaptive devices to help their peers. The group created the device from every day items, like a plastic cup, and pieces they created on a 3D printer. The device can be connected to a number of different switches like a button of a pad, depending on the need. Wednesday, April 23, 2025, Bethel, Conn.
H John Voorhees III/Hearst Connecticut Media
An agency called Ability Beyond provides services for people in New York and Connecticut who have a range of disabilities, including mobility and communication challenges. Laurie Dale, the agency’s senior leader of assistance technology solutions, is hoping that technology like 3D printing will help with some of the barriers these people face, but took it a step further. She heads a local effort called the TIP Squad (Technology Innovations for Peers), in which young adults with disabilities are actually helping to come up with, and manufacture, assistive solutions that can help improve quality of life for themselves and their peers. In addition to 3D printing, they learn skills like circuitry and soldering to build their devices, and they also test out what’s already on the market, often taking apart devices and rebuilding them with adaptable components. Other than the printers themselves, what they use to create their devices is very low-cost, like drag-and-drop software and free open source templates. Thanks to $32,000 in grant funding from Verizon, the TIP Squad has been able to grow. The group also serves as a workplace training program for its participants.
Dale explained, “They’re working on a lot of soft skills, things that will help you prepare for employment in the community: Coming in on time, working together as a group, as a team. Following directions together, wearing the uniform.
“Sometimes it’s the first time people are being required to do things like that. So it’s a great chance to get ready for employment.”
Subscribe to Our Email Newsletter
Stay up-to-date on all the latest news from the 3D printing industry and receive information and offers from third party vendors.