We’ve got some more news from last week’s RAPID+TCT to kick off today’s 3D Printing News Briefs, and then moving on to some interesting pieces of military AM news. Read on for all the details!
SME Announces AM Awards & AM Pitchfest Winners
Throughout RAPID+TCT last week, nonprofit SME announced the winners of its 2025 Additive Manufacturing (AM) Awards and AM Pitchfest, given to celebrate the accomplishments of companies, individuals, and teams that have significantly impacted AM commercialization. First, the Digital Manufacturing Challenge recognizes the work of student teams who design, build, and use infrastructure-level systems that deploy manufacturing solutions in renewable energy, advanced manufacturing, and sustainability. The team from DuPont Manual High School won for its “Sustainable and Effective Composite Repairs Using Novel 3D Printed Patch Designs,” while the Rensselaer Polytechnic Institute & Cornell University undergraduate team won for a “Micro Solar-based Steam-Powered Desalination Plant.” The graduate team from the University of Georgia won for “Fabrication of Wind Turbine Blade Solid Wastes for High-Performance Composite Fibers.” Moving on, the Aubin AM Case Study Award, which recognizes innovative AM use cases, was given to Dimensional Energy and Oak Ridge National Laboratory (ORNL) for their “Binder Jet Additive Manufacturing of Silicon Carbide Reactor Assemblies.” The runner-up was the team from Norsk Titanium and The Boeing Company for “RPD® By The Numbers.”
The AM Startup Award is given to young companies that have developed an AM application or technology that uses a unique approach or solves an existing problem. 3D Architech was the winner for its “High-resolution Metal Manufacturing for Energy Efficiency,” and the two runners-up were AMIS and Snowbird Technologies. The AM Pitchfest competition is open to startups, academic spinoffs, and entrepreneurs that bring emerging products, technology, and applications to the market. Solideon won for “Build Hardware at the Speed of Software,” and was given the chance to exhibit at RAPID in a fully equipped booth; the runner-up for this award was Kupros, Inc. Finally, John Barnes, founder and president of The Barnes Global Advisors and co-founder and CEO of Metal Powder Works, was given the AM Industry Achievement Award. This recognizes a team or individual for their outstanding accomplishments, used in a commercial or industrial environment, that majorly impact the adoption of AM in any industry.
Our congratulations to all the winners!
Phase3D Completes Air Force Cold Spray Inspection System Deployment
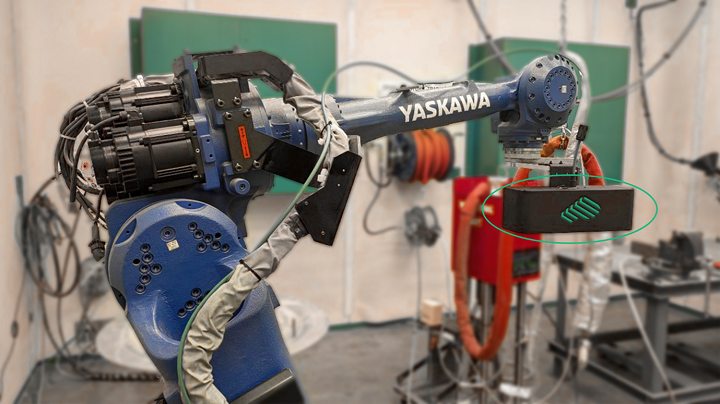
Fringe Inspection™: Cold Spray attaches to the robotic control arm and scans cold spray deposits during the 3D printing process.
Backed by $1.25 million from the Air Force Research Laboratory (AFRL), advanced 3D measurement technologies leader Phase3D has created and deployed its Fringe Inspection: Cold Spray system, marking a big step in real-time, in-situ inspection for improving reliability and precision in aerospace and defense applications. Cold spray AM is used for repair and production across both of these sectors, but ensuring reliable, consistent quality has been an issue. Phase3D’s Fringe Inspection system, targeted here for cold spray AM, uses structured light technology to enhance quality control (QC) by providing real-time deposit inspection. The system offers real-time detection of defects like pitting, cratering, and cracking (seen in this article’s featured image); assesses and measures spray deposit surfaces to verify repair quality; and allows technicians to optimize everything by inspecting and dynamically adjusting the cold spray process. In order to successfully confirm its effectiveness in enhancing QC for aerospace and military applications, Fringe Inspection: Cold Spray was tested and validated in an operational setting at the University of Dayton Research Institute (UDRI) and Ellsworth Air Force Base.
“The successful completion of this project underscores the importance of real-time inspection in additive manufacturing. The deployment at Ellsworth AFB proves that structured light inspection is a game-changer for cold spray applications,” said Phase3D’s Founder and CEO Niall O’Dowd. “This technology not only ensures higher-quality repairs but also delivers significant cost and time savings for the Air Force.”
This project was conducted under the STTR Phase II Proposal F2-16465 – In-Situ Monitoring for Blown Powder Additive Manufacturing contract, and achieved several important milestones. Phase3D is now expanding the applications of structured light inspection across AM and industrial repair sectors, and collaborating with the Department of Defense and private industry partners to further improve cold spray repair capabilities.
3D CAD Models & AM Improving Army Ground Vehicle Readiness
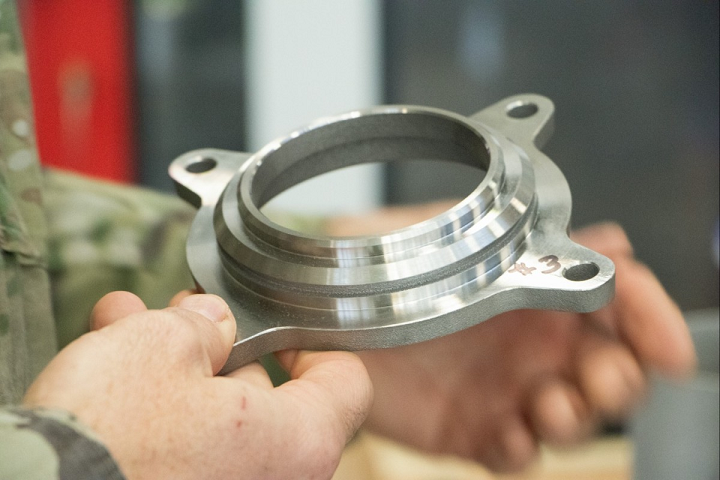
A newly produced Battle Damaged Repair & Fabrication part made at the Advanced Manufacturing Center of Excellence inside the Rock Island Arsenal-Joint Manufacturing and Technology Center. The BDR&F program allows 3D printing technology to produce replacement parts quickly and get military vehicles back into the field faster. Rock Island Arsenal-Joint Manufacturing and Technology Center develops, manufactures and delivers readiness solutions through conventional and advanced manufacturing processes for the U.S. Army and Department of Defense systems globally. (Photo Credit: Kendall Swank)
The Battle Damage Repair and Fabrication (BDRF) effort, led by the U.S. Army Tank-automotive Armaments Command (TACOM), is using additive manufacturing to quickly replace damaged Army ground vehicle parts, which decreases vehicle down-time in formations and supports readiness. By using 3D CAD models and 3D printers to make temporary replacements for parts that are obsolete or have long lead times, the process is helping to reduce the Army’s overall logistics burden, and lengthen the lifespan of older platforms. For the past year, the U.S. Army DEVCOM Ground Vehicle Systems Center (GVSC)—with help from Rock Island Arsenal’s Joint Manufacturing and Technology Center (RIA-JMTC)—has supported TACOM and its Integrated Logistics Support Center (ILSC) through assessments of over 40,000 vehicle parts, resulting in the development of more than 600 3D CAD models. Scans of these parts are uploaded to a database, and their 3D printed replacements are used temporarily to help keep battle-worn vehicles operational for longer. Some of the temporary replacement parts that have come out of the BDRF program have even been shown to outperform the originals in tests, and were submitted to the program manager for consideration as a more permanent secondary supply source.
“Units are installing those parts on vehicles and bringing equipment back to mission-capable status. In collaboration with our partners, we hope to use 3D printing and other advanced manufacturing techniques to generate readiness as far forward on the field as possible,” said Michael Hansen, TACOM’s advanced manufacturing lead.
3D Printed Kamikaze Drone Completes Flight on U.S. Army Test Range
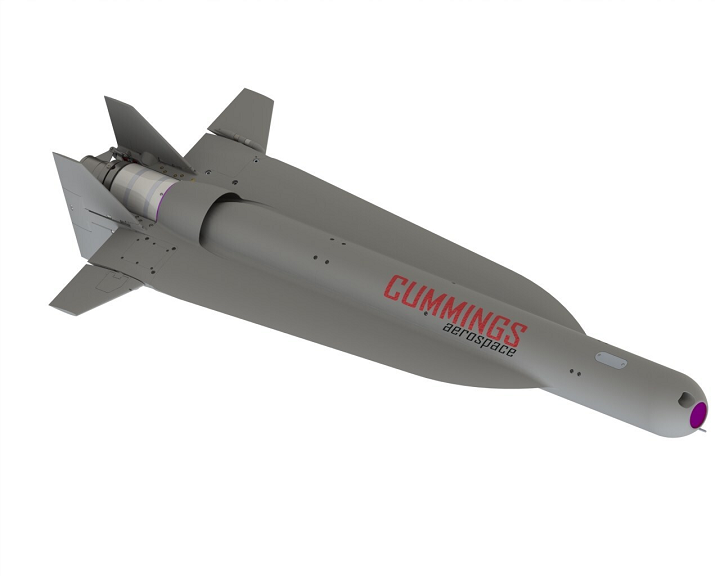
Hellhound is a turbo-jet-powered, 3D printed kamikaze drone that can fly faster than 375 miles per hour. Hellhound is designed to equip the U.S. Army’s Infantry Brigade Combat Teams with the same lethal combat power as Armored Brigades. (Rendering of Hellhound provided by Cummings Aerospace)
Finally, Alabama-based Cummings Aerospace, a Native American Woman-Owned Small Business, announced that its 3D printed, turbojet-powered Hellhound S3 kamikaze drone completed its first demonstration flight during the Army Expeditionary Warrior Experiment (AEWE) 2025 at Fort Moore, Georgia. This was the first flight of the unmanned aircraft system (UAS) on a U.S. Army test range, which demonstrates its tactical proficiency in an operation environment. The Hellhound S3, with its modular design, was designed to give the Army’s Infantry Brigade Combat Teams (IBCTs) the same combat power as Armored Brigades have, so the teams can carry out precise, long-range strikes against armored vehicles, tanks, and fortified positions. At the AEWE, the drone, which weighs less than 25 pounds and can reportedly fly at speeds of over 375 mph, completed a GPS-guided tactical mission using an inert warhead payload. This not only revalidated its airframe and key subsystems at Technology Readiness Level 7, but also gave company engineers a chance to gather important feedback from warfighters.
“Hellhound’s performance at AEWE 2025 highlighted a fundamental reality — speed matters, and quadcopters and prop-driven drones take too long to get downrange. While quadcopters and propeller-driven drones will still be puttering along behind friendly lines, Hellhound will already be over the target area, giving IBCTs the ability to strike faster, reach deeper into the battlespace, and decisively engage fleeting, time-sensitive targets,” stated Cummings Aerospace CEO Sheila Cummings.
Cummings Aerospace will conduct additional flight tests of the Hellhound S3 over the coming months, and plans to submit a proposal formally offering the UAS to U.S. Army’s Low Altitude Stalking and Strike Ordnance (LASSO) program.
Subscribe to Our Email Newsletter
Stay up-to-date on all the latest news from the 3D printing industry and receive information and offers from third party vendors.